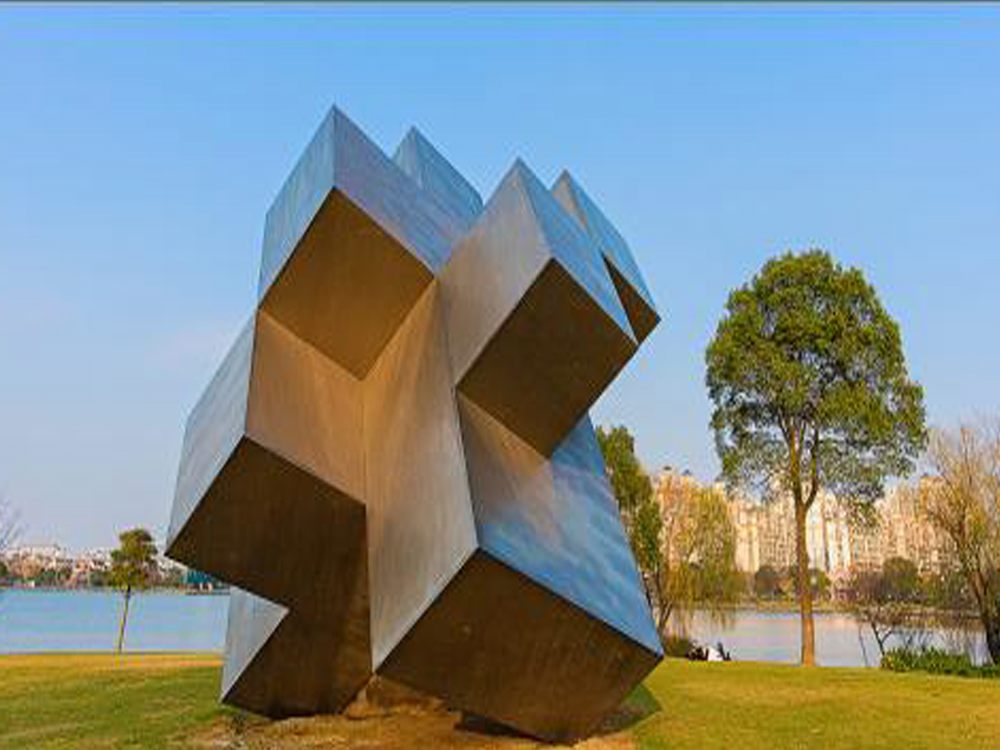
The porcelain sculpture supply chain is a meticulous process that transforms raw materials into exquisite works of art. Understanding its critical stages ensures quality and efficiency in production.
1. Material Selection: The foundation of any porcelain sculpture lies in high-quality kaolin clay and other additives. Purity and consistency directly impact the final product's durability and aesthetic appeal.
2. Design and Prototyping: Artists and designers create detailed sketches or 3D models, refining proportions and artistic elements before production begins.
3. Molding and Shaping: Skilled artisans use slip casting, hand-building, or wheel-throwing techniques to shape the clay into the desired form, ensuring precision and detail.
4. Drying and Bisque Firing: The sculpture is air-dried to remove moisture before undergoing bisque firing at lower temperatures to harden the clay without vitrifying it.
5. Glazing and Decoration: Artisans apply glazes and hand-paint intricate designs, adding color and texture. This stage demands expertise to avoid imperfections.
6. Final Firing: The piece is fired at high temperatures (1200–1400°C) to achieve strength and translucency, a make-or-break phase where cracks or warping can occur.
7. Quality Control and Finishing: Each sculpture is inspected for flaws, polished, and sometimes hand-finished to meet artistic and functional standards.
8. Packaging and Distribution: Secure packaging ensures safe transit, while logistics partners deliver the fragile artwork to galleries, retailers, or collectors worldwide.
Mastering these stages is essential for producing durable, visually stunning porcelain sculptures that uphold tradition while meeting modern demands.