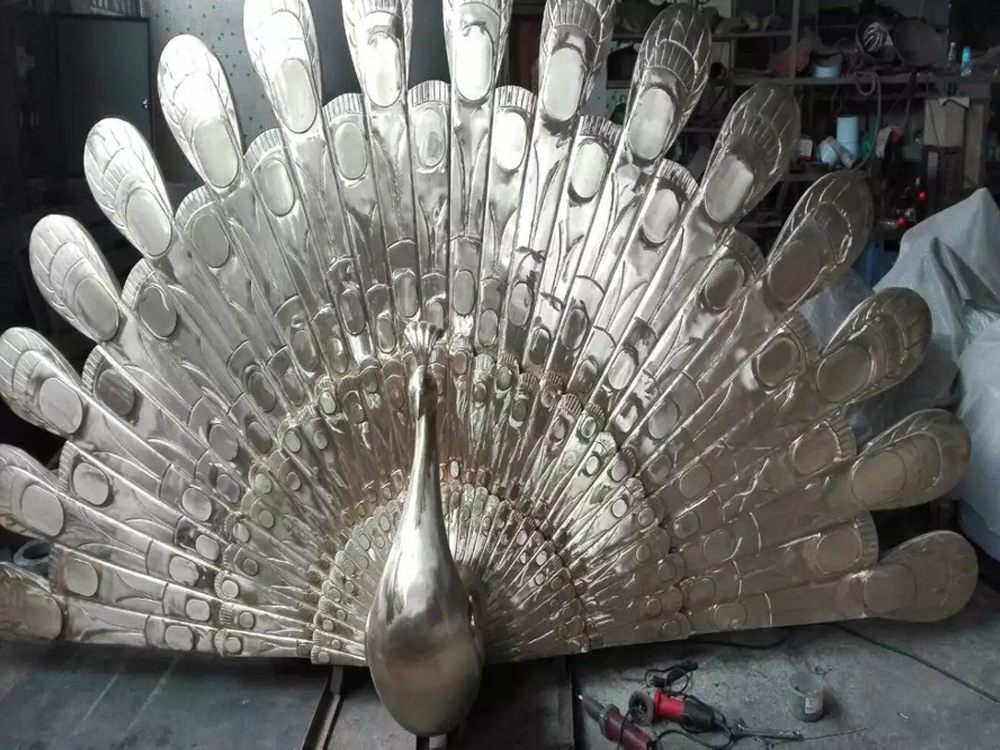
Creating porcelain sculptures with integrated mechanical components is a fascinating yet demanding endeavor that blends artistry with engineering. One of the primary challenges is the inherent fragility of porcelain, which requires meticulous handling during both the sculpting and assembly phases. The material’s sensitivity to stress and temperature fluctuations can lead to cracks or breaks, especially when incorporating moving parts.
Another significant hurdle is achieving precise alignment between the ceramic elements and mechanical components. Porcelain shrinks during firing, making it difficult to ensure that gears, hinges, or other mechanisms fit perfectly post-kiln. Artists and engineers must account for this shrinkage in their designs, often through iterative prototyping.
Additionally, the aesthetic integrity of the sculpture must be preserved while accommodating functional mechanics. Balancing form and function without compromising the delicate beauty of porcelain demands innovative solutions, such as hidden joints or custom-fabricated parts.
Lastly, the durability of mechanical components within a porcelain structure is a concern. Wear and tear over time can affect both the movement and the ceramic’s surface, requiring materials that harmonize in longevity. These challenges highlight the intricate dance between tradition and technology in this unique art form.