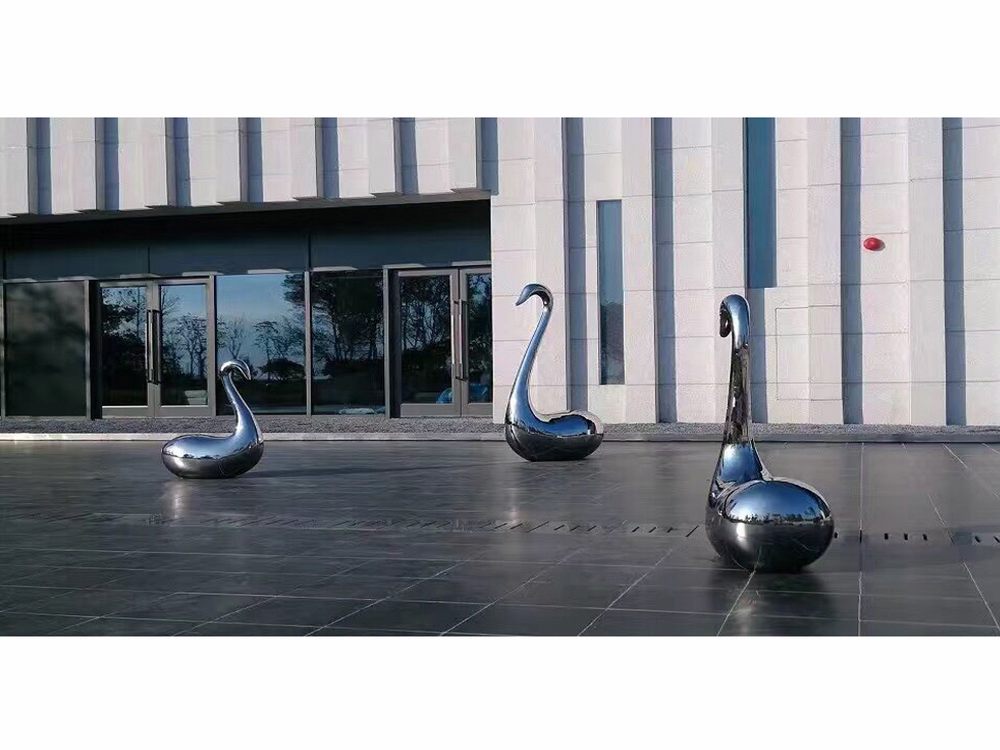
Creating large-scale porcelain sculptures presents unique challenges, particularly in maintaining structural integrity. Artists employ a combination of technical expertise and creative problem-solving to prevent weaknesses in these delicate works.
The foundation lies in material preparation. Experienced ceramicists often blend porcelain with small amounts of other clays or grog to improve tensile strength while retaining the material's signature translucency. This careful balancing act requires extensive testing to determine optimal mixtures for different scales.
Construction techniques prove equally critical. Many artists build sculptures in sections using coil, slab, or press-mold methods, allowing each component to partially dry before assembly. Strategic internal supports—sometimes removable metal armatures or permanent ceramic stays—provide stability during both construction and firing.
Kiln firing demands precise control. Large pieces often require slower bisque firings with extended temperature plateaus to ensure even moisture removal. Glaze firings may involve multiple stages with careful cooling periods to prevent thermal shock. Some artists employ custom-built kilns or sectional firing for exceptionally large works.
Innovative drying methods help prevent cracks. Controlled humidity environments, plastic wrapping, and gradual exposure to air allow uniform shrinkage. Advanced artists sometimes use computer modeling to predict stress points before construction begins.
The most successful large-scale porcelain sculptures result from this meticulous attention to every stage—from material selection through final firing—combined with an artist's intimate understanding of porcelain's unique behavior under stress and heat.