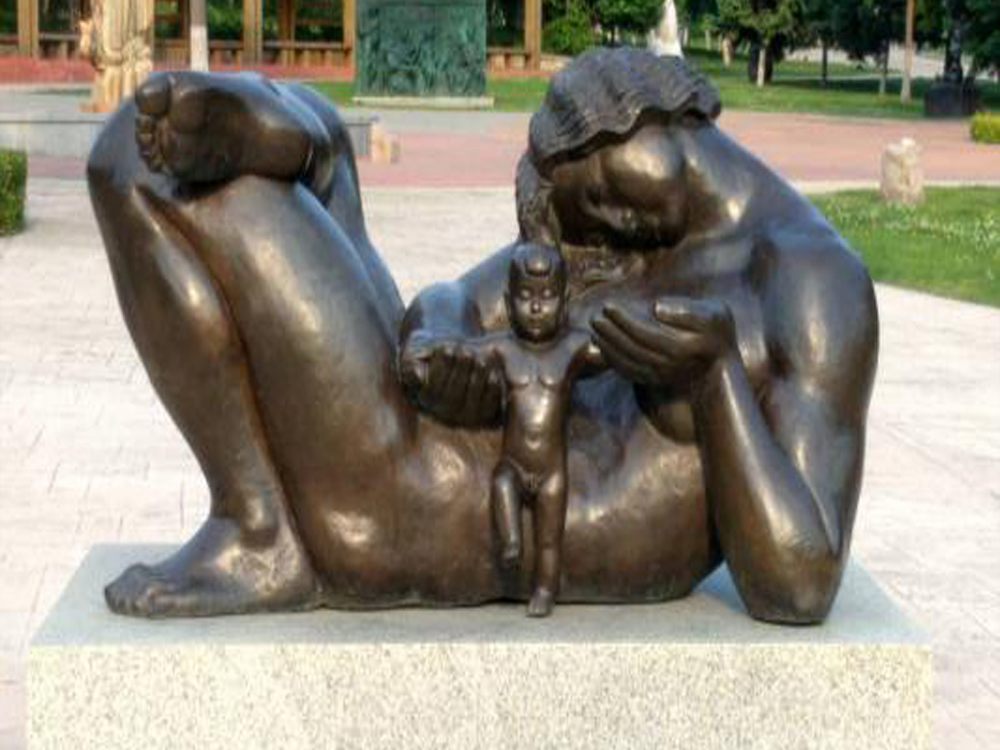
Glaze pinholing is a common yet frustrating issue in porcelain sculpture production, where tiny holes or craters form in the glaze surface during firing. Artists and manufacturers employ a multi-faceted approach to address this problem, combining material science, kiln mastery, and creative adaptations.
The root causes often trace back to trapped gases, improper glaze viscosity, or contamination. Experienced ceramicists mitigate this by carefully controlling bisque firing temperatures to ensure thorough burnout of organic materials. Many adjust glaze formulations, adding fluxes like frit or silica to improve melting behavior and reduce surface tension.
Kiln technicians emphasize the importance of controlled firing cycles, particularly during the critical quartz inversion phase (573°C). Slow cooling rates between 800-600°C allow proper glaze settling, while oxidation firing helps combust residual carbon. Some studios introduce "soaking" periods at peak temperature to heal surface imperfections.
Contemporary solutions include using computer-controlled kilns with precise ramp rates, or applying multiple thin glaze layers rather than single thick coatings. For stubborn cases, artists may embrace the aesthetic, incorporating pinholing into textured designs or filling imperfections with gold lacquer in the kintsugi tradition. Manufacturers often implement rigorous material testing protocols, examining clay body composition and glaze fit through thermal expansion matching.
The most successful practitioners combine technical knowledge with artistic flexibility, viewing each firing as both a scientific experiment and creative opportunity. By understanding the complex interplay of materials, heat, and time, they transform potential defects into either flawless finishes or intentional artistic statements.