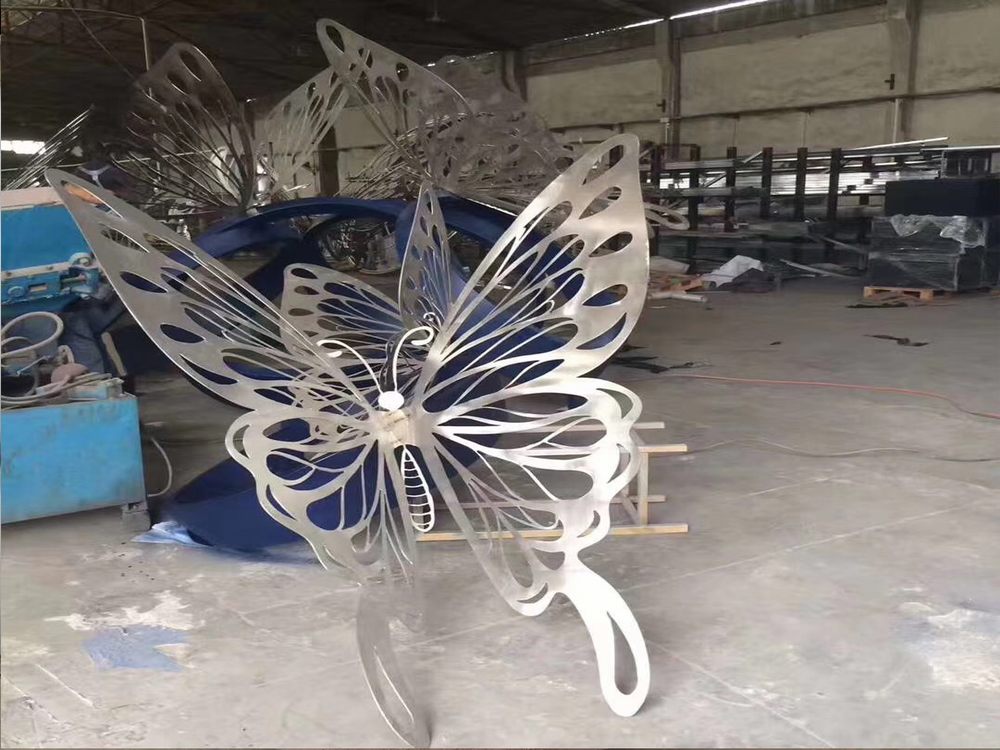
Creating porcelain sculptures that endure outdoor conditions requires a meticulous blend of material science and artistic craftsmanship. Artists begin by selecting high-quality porcelain clay with low porosity, often mixed with additives like grog or alumina to enhance structural integrity. The sculpting process involves building thick-walled forms to resist thermal shock, with careful attention to avoiding sharp edges that could chip.
The key to durability lies in the firing process. Pieces undergo bisque firing at lower temperatures (900-1000°C) to remove moisture, followed by high-fire glazing at 1200-1400°C to vitrify the clay body. Artists use specialized outdoor glazes containing silica and metallic oxides that create an impermeable surface, often applying multiple layers for added protection.
Advanced techniques include:
1. Crystalline glazes that form weather-resistant mineral structures
2. Salt firing for dense, textured surfaces
3. Post-firing sealants like marine-grade epoxy for extreme climates
Successful outdoor porcelain sculptures also incorporate drainage systems in their bases to prevent water accumulation and frost damage. Many artists test prototypes through seasonal cycles before final installation, ensuring their creations can withstand decades of exposure to sun, rain, and temperature fluctuations while maintaining their aesthetic appeal.