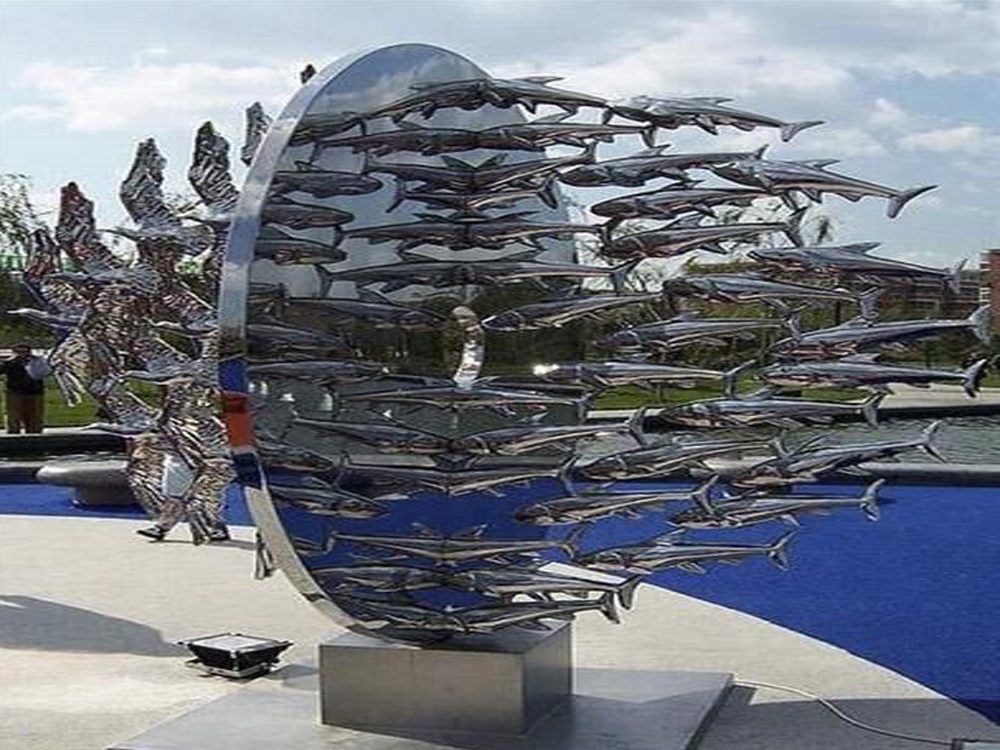
Creating porcelain sculptures with complex, multi-part assemblies presents unique challenges that test even seasoned ceramic artists. One major hurdle is material fragility—porcelain's delicate nature demands meticulous handling during shaping and joining to avoid cracks or breaks. Shrinkage during drying and firing adds another layer of complexity, as different components may contract at varying rates, leading to misalignment.
The assembly process itself requires precision, as poorly fitted joints weaken structural integrity. Artists must master specialized adhesives or slip-and-score techniques while accounting for each piece's weight distribution. Firing multi-part sculptures proves particularly demanding, with thermal stress potentially causing warping or fractures if heating/cooling rates aren't perfectly calibrated.
Glazing presents further complications, as pooled glaze can fuse moving parts, while inconsistent application may create visual disharmony. Many artists address these challenges through segmented firing strategies, custom-designed support systems, and rigorous clay body testing—proving that overcoming these obstacles yields breathtaking artistic achievements.