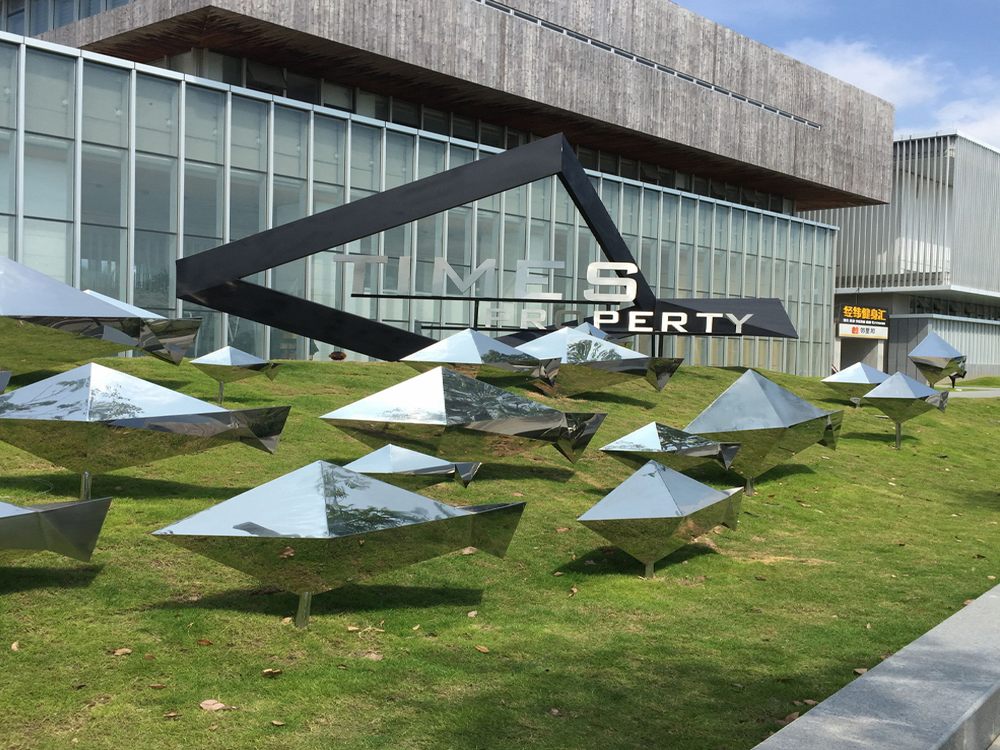
Achieving precise color matching in porcelain sculptures is a complex process fraught with challenges that test the limits of artistic and technical skill. One of the primary obstacles is the inherent variability of raw materials. Clay composition, mineral impurities, and even water content can subtly alter the final hue after firing, making consistency difficult to achieve.
Glaze chemistry presents another layer of complexity. The interaction between pigments, fluxes, and silica under high temperatures often yields unpredictable results. A slight deviation in the kiln's atmosphere—whether oxidation or reduction—can dramatically shift colors, turning an intended cobalt blue into an unintended violet or green.
Firing temperature precision is equally critical. Porcelain requires exact thermal control, as even a 10-degree Celsius variation can affect color development. Many artists rely on pyrometric cones and digital controllers, yet the kiln's hot and cold spots still introduce inconsistencies.
Additionally, the artist's vision must account for how glazes mature differently at various thicknesses. A brushstroke's weight or a dip's duration can change the depth and tone of the applied color. This demands not only technical mastery but also an intuitive understanding of material behavior.
Modern solutions like computer-aided pigment measurement and standardized firing protocols help mitigate these issues. However, the alchemy of porcelain ensures that each piece retains a unique character—a testament to both the challenges and the enduring allure of this ancient art form.