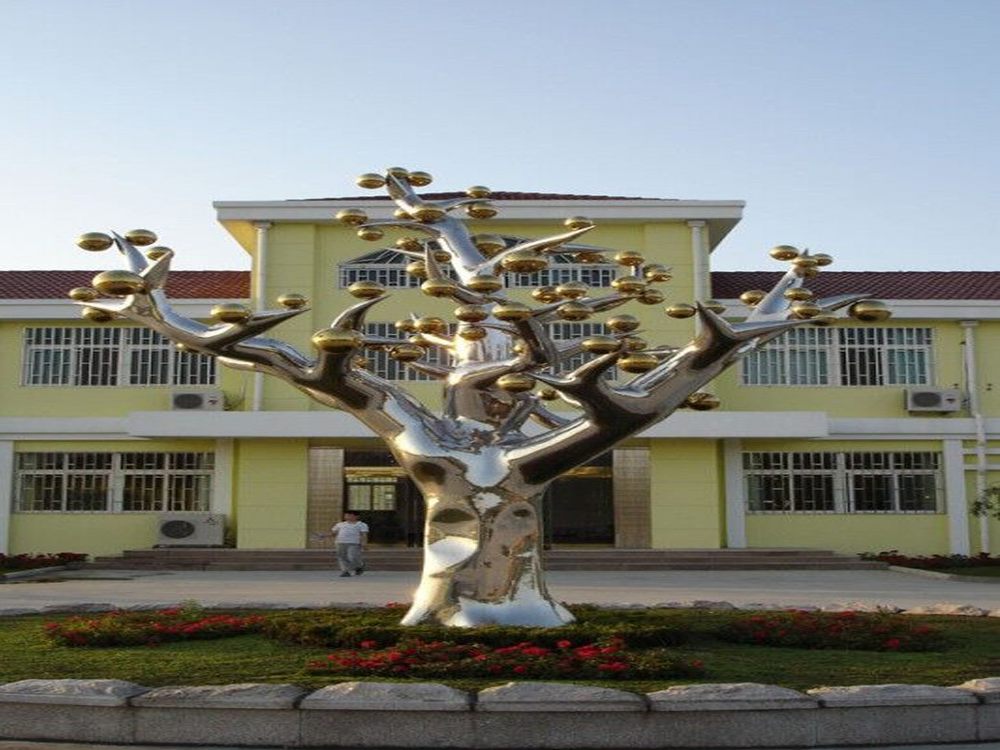
Ceramic artists face a common yet critical challenge: shrinkage during the drying and firing stages. As clay loses moisture and undergoes high-temperature firing, it contracts, often leading to cracks or warping. To address this, skilled potters employ several strategies.
First, they carefully control the drying process by wrapping pieces in plastic or using damp boxes to slow moisture evaporation, ensuring even contraction. Wedging clay thoroughly removes air pockets, reducing uneven shrinkage. Adding grog (pre-fired clay particles) or sand to the clay body also minimizes contraction by providing structural support.
During firing, artists use controlled kiln ramping—gradually increasing temperature—to prevent thermal shock. Bisque firing at lower temperatures before glaze firing further stabilizes the clay. Additionally, precise measurements account for expected shrinkage (typically 10-15%), allowing artists to scale designs accordingly.
Mastering these techniques ensures finished ceramics retain their intended form, turning potential flaws into flawless artistry.