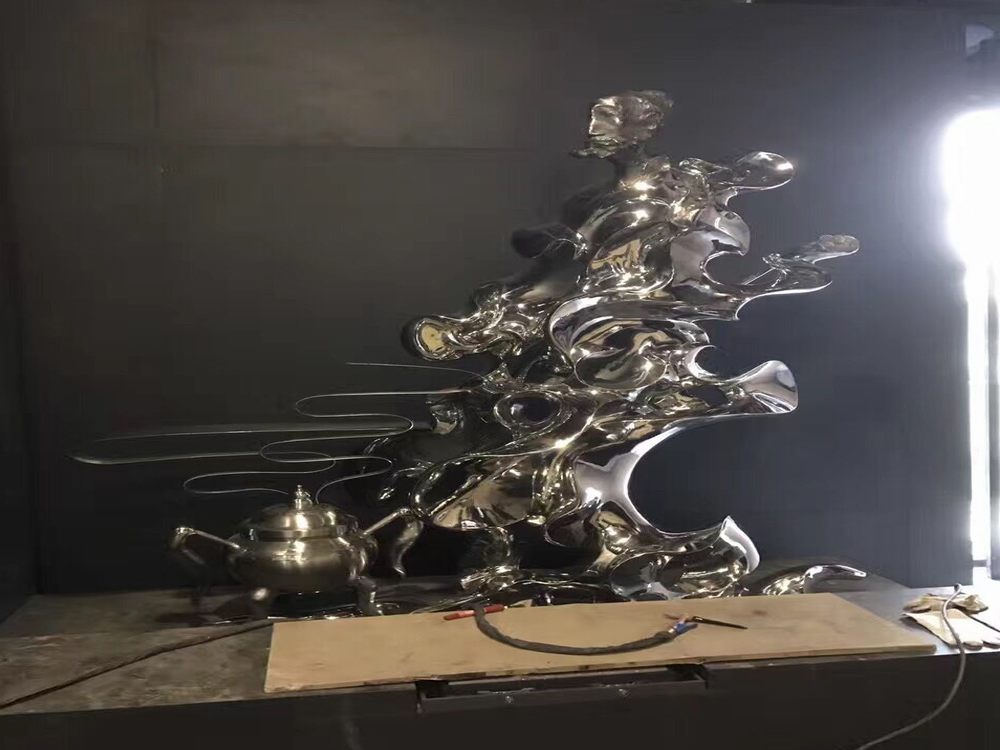
Achieving uniform glaze colors across multiple production batches is a persistent challenge in ceramic manufacturing. One major hurdle lies in raw material variability—natural minerals and pigments often differ slightly in composition, leading to subtle color shifts. Firing conditions further complicate consistency, as even minor temperature fluctuations or kiln atmosphere changes can alter glaze chemistry and final hues.
The precision of mixing also plays a critical role. Small measurement errors when combining multiple pigments compound into noticeable color differences. Additionally, application thickness variations affect how light interacts with the glaze surface, creating perceived color changes even with identical formulations.
Industrial-scale production introduces logistical challenges too. Large batches may stratify during storage, while different production dates expose materials to varying humidity levels that influence glaze behavior. Manufacturers combat these issues through rigorous quality control systems, standardized testing protocols, and advanced spectrophotometric analysis—yet perfect consistency remains an elusive goal requiring constant vigilance across the entire production chain.