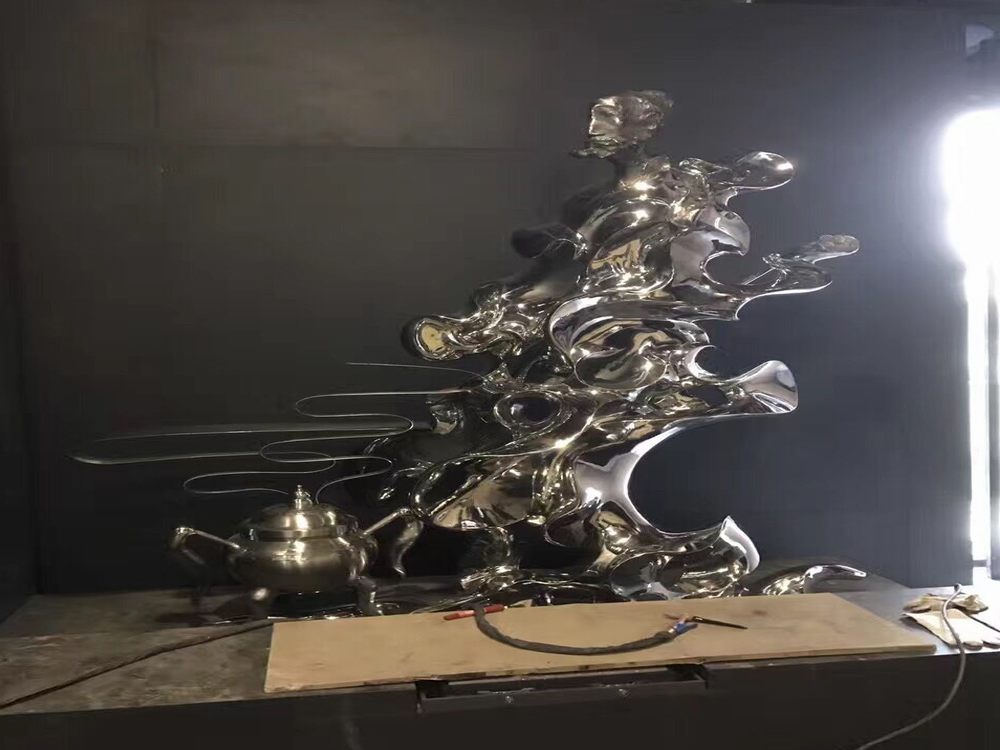
Achieving a consistent glaze application on complex ceramic forms is a nuanced process that often presents several challenges. One of the primary issues is uneven coverage due to the intricate geometry of the piece. Recessed areas may trap excess glaze, while raised sections might receive too little, leading to an inconsistent finish.
Another common challenge is controlling the glaze thickness. Complex forms often require multiple dipping or spraying sessions, which can result in uneven layers if not meticulously managed. Additionally, the viscosity of the glaze plays a critical role; too thick, and it may not flow into crevices, too thin, and it might run off high points.
Firing inconsistencies further complicate the process. Variations in kiln temperature or uneven heat distribution can cause the glaze to react differently across the form, leading to blotches or color shifts. Lastly, the choice of glaze type—whether matte, glossy, or crystalline—can impact its behavior on complex surfaces, requiring tailored application techniques.
To mitigate these challenges, potters often experiment with application methods like spraying, brushing, or dipping, adjusting glaze recipes, and refining firing schedules. Mastery comes with practice, but understanding these hurdles is the first step toward achieving flawless results.