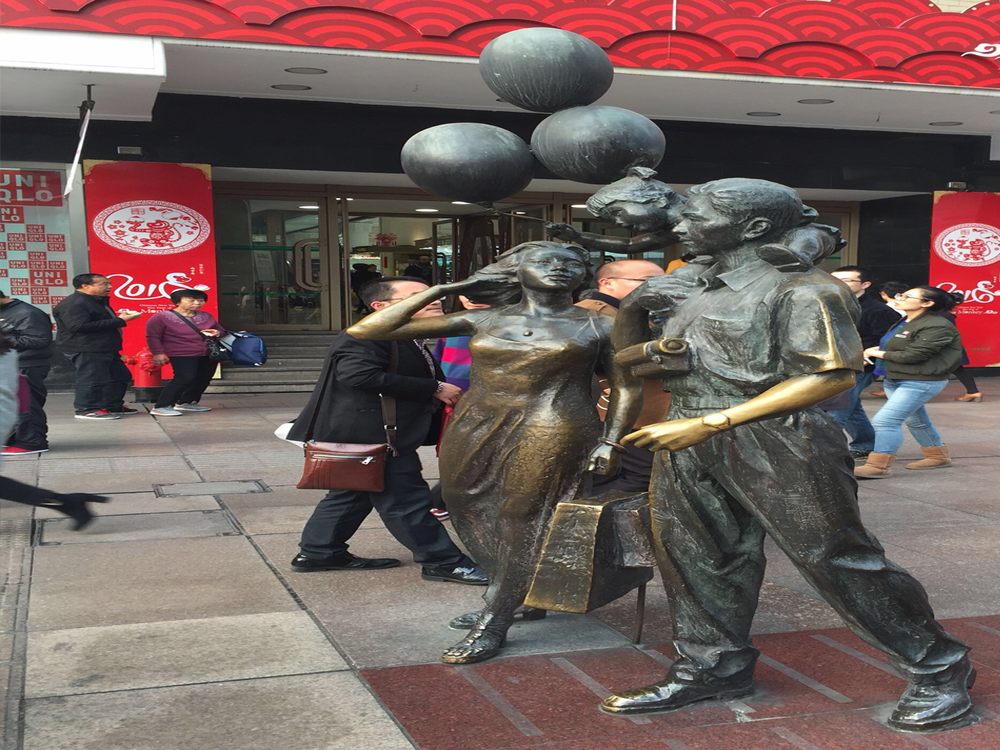
Glaze crazing, the fine network of cracks that can appear on porcelain sculptures, is a common challenge for both artists and manufacturers. While some view it as a flaw, others embrace it as an aesthetic feature. However, when unintended, it can compromise the structural integrity and longevity of the piece.
To address this issue, ceramic artists often adjust the composition of their glazes. By carefully balancing the thermal expansion coefficients of the clay body and the glaze, they reduce the mismatch that causes cracking. Some opt for specially formulated "fit glazes" designed to expand and contract at similar rates to the underlying clay.
Manufacturers employ precise kiln firing schedules, gradually cooling pieces to minimize stress. Advanced techniques like double firing, where the bisque and glaze firings are meticulously controlled, help prevent crazing. Post-production, epoxy or resin fillers may be used to stabilize existing cracks in high-value pieces.
Contemporary solutions include nano-material additives that increase glaze elasticity, while traditionalists may use time-tested recipes with higher silica content. Whether viewed as a defect or a design element, understanding and controlling glaze crazing remains essential in porcelain artistry.