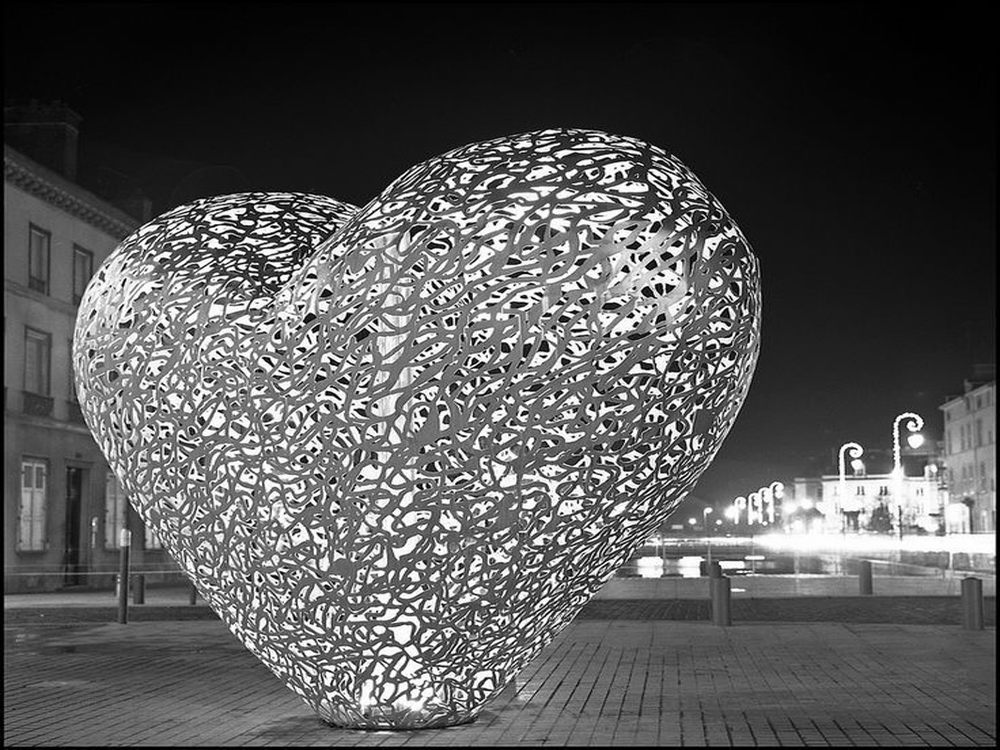
Creating a flawless join in multi-piece porcelain sculptures is a delicate art that demands precision and expertise. One of the most significant challenges is material compatibility—ensuring the adhesive or clay slip matches the original porcelain’s composition to prevent cracking or discoloration over time. Shrinkage during drying and firing can also disrupt alignment, requiring meticulous calculations to account for dimensional changes.
Another hurdle is achieving invisible seams, as even minor imperfections become glaring under glaze. Artists must master techniques like slip-trailing or needle-tool blending to disguise joins. Structural integrity is equally critical; weak bonds may fail under stress, especially in large or intricate pieces.
Environmental factors like humidity and temperature further complicate the process, affecting drying times and adhesion. Finally, restoration of antique porcelain introduces additional variables, such as aging materials and historical accuracy. Overcoming these challenges requires a blend of scientific knowledge, artistic skill, and patience to preserve the sculpture’s aesthetic and functional unity.