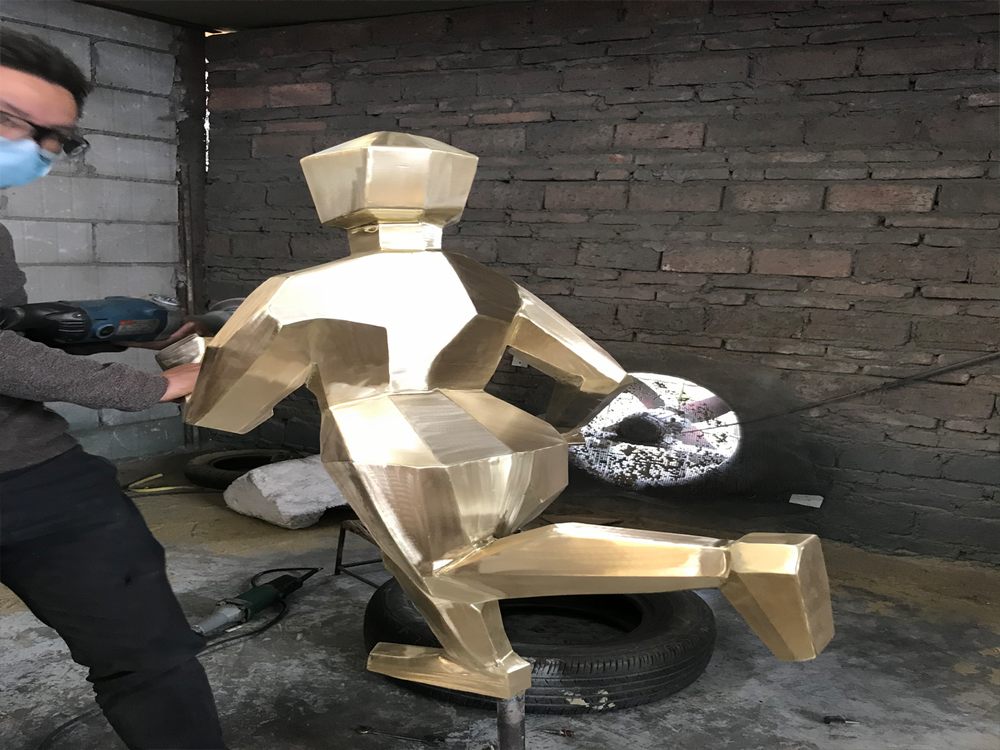
Creating porcelain sculptures with vibrant colors while maintaining durability is a complex challenge for ceramic artists. The primary obstacle lies in the high firing temperatures required for porcelain, which often cause traditional pigments to fade or degrade. Achieving rich hues demands a delicate balance between glaze chemistry and kiln conditions, as excessive heat can dull colors or create instability in the ceramic body.
Another challenge is the interaction between glazes and the porcelain surface. Some bright pigments contain metals that may weaken the sculpture's structural integrity over time. Artists must carefully select materials that bond well with porcelain without causing cracks or surface defects. Additionally, color intensity often diminishes during the cooling process, requiring precise control of temperature reduction rates.
Innovative techniques like underglaze painting and layered firing can help preserve vibrancy, but these methods increase production time and cost. Modern advancements in ceramic chemistry offer new possibilities, yet finding non-toxic, durable solutions remains an ongoing pursuit in the art world. Ultimately, mastering this balance between aesthetics and longevity defines the skill of a true porcelain artist.