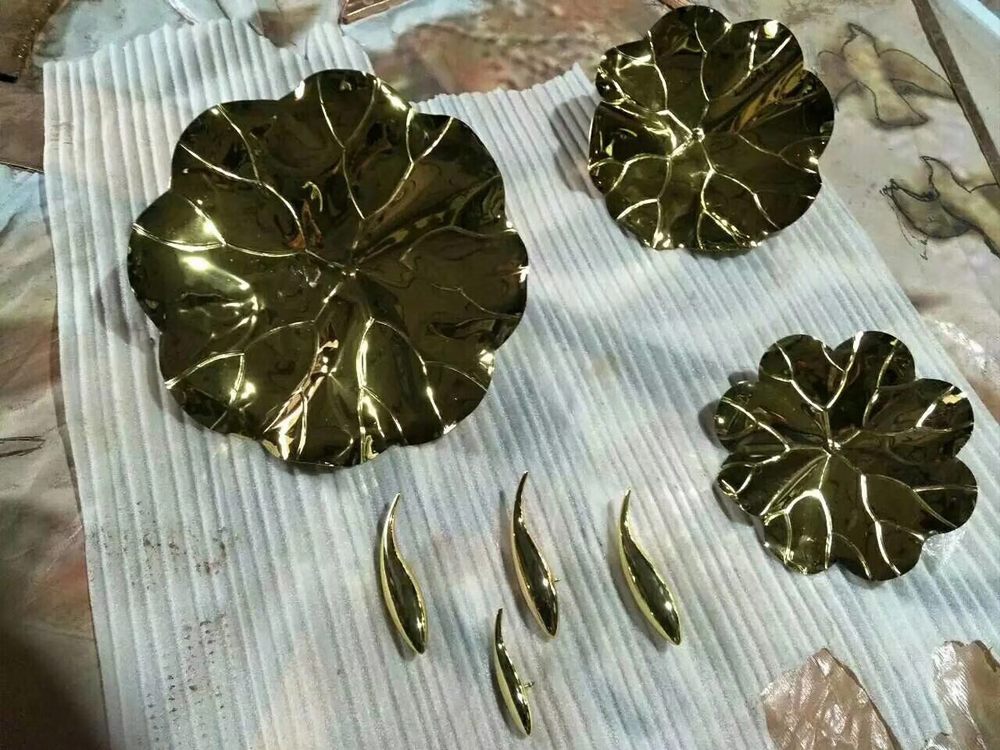
The porcelain sculpture industry, renowned for its delicate artistry and craftsmanship, relies heavily on kaolin clay as a primary raw material. Recent fluctuations in global kaolin supply have sent ripples through this niche market, impacting everything from production costs to artistic expression.
Supply chain disruptions caused by geopolitical tensions, environmental regulations, and mining challenges have led to volatile pricing. Many studios report kaolin costs rising by 20-30% in recent years, forcing difficult choices between absorbing expenses or passing them to collectors. The finest white kaolin deposits, particularly those from historically stable sources like Cornwall and Georgia, have become increasingly precious commodities.
Artists face creative constraints as certain clay grades become scarce. Traditional porcelain techniques requiring specific plasticity and whiteness must sometimes be adapted, leading to both challenges and unexpected innovations. Some sculptors are experimenting with alternative clay blends, while others stockpile preferred materials, altering cash flow dynamics.
Gallery owners note collectors growing more discerning about material provenance, with works using premium kaolin commanding higher prices. This bifurcation in the market creates both opportunities for premium positioning and challenges for emerging artists.
The industry's future may lie in diversified sourcing, including developing deposits in Africa and Southeast Asia, though quality consistency remains a concern. Technological solutions like advanced material testing and clay blending algorithms are helping studios maintain quality standards despite supply inconsistencies.
As the porcelain art world navigates these material uncertainties, one truth emerges: the value of skilled artisans who can transform even imperfect materials into objects of beauty has never been higher. The current challenges may ultimately spur a new era of technical innovation in ceramic arts.