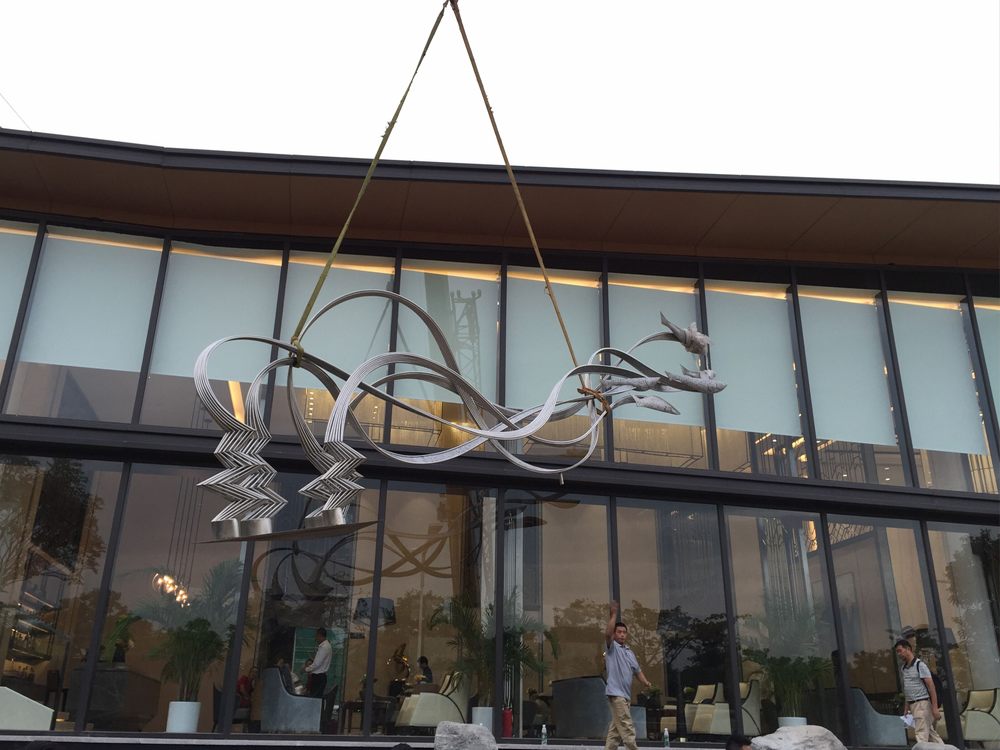
Producing porcelain sculptures on a large scale without compromising artistic quality presents a unique set of challenges that blend technical precision with creative finesse. The first major hurdle lies in material consistency—porcelain clay must maintain uniform composition and moisture levels across thousands of pieces, as even minor variations can affect firing results and final appearance.
Skilled labor shortages compound these difficulties, as mass production requires artisans who can replicate intricate designs with machine-like consistency while preserving each piece's handmade character. The delicate nature of unfired porcelain demands extreme care during molding and handling, with even slight pressure potentially distorting fine details.
Firing processes introduce another layer of complexity. Kiln temperature variations across large batches can create inconsistencies in color, texture, and structural integrity. Manufacturers must balance production speed with the slow, careful drying porcelain requires to prevent cracking—a process that resists industrialization.
Perhaps most challenging is maintaining artistic vision at scale. While molds enable reproduction, they gradually degrade with use, subtly altering details. Successful manufacturers implement rigorous quality control, often combining modern technology with traditional techniques, such as using 3D scanning to monitor mold integrity while preserving hand-finishing for critical details.
The solution often lies in strategic compromises—standardizing certain elements while reserving handwork for signature features, or creating limited editions that balance accessibility with artistic value. Those who master this balance can bring porcelain art to wider audiences without diminishing its aesthetic power.