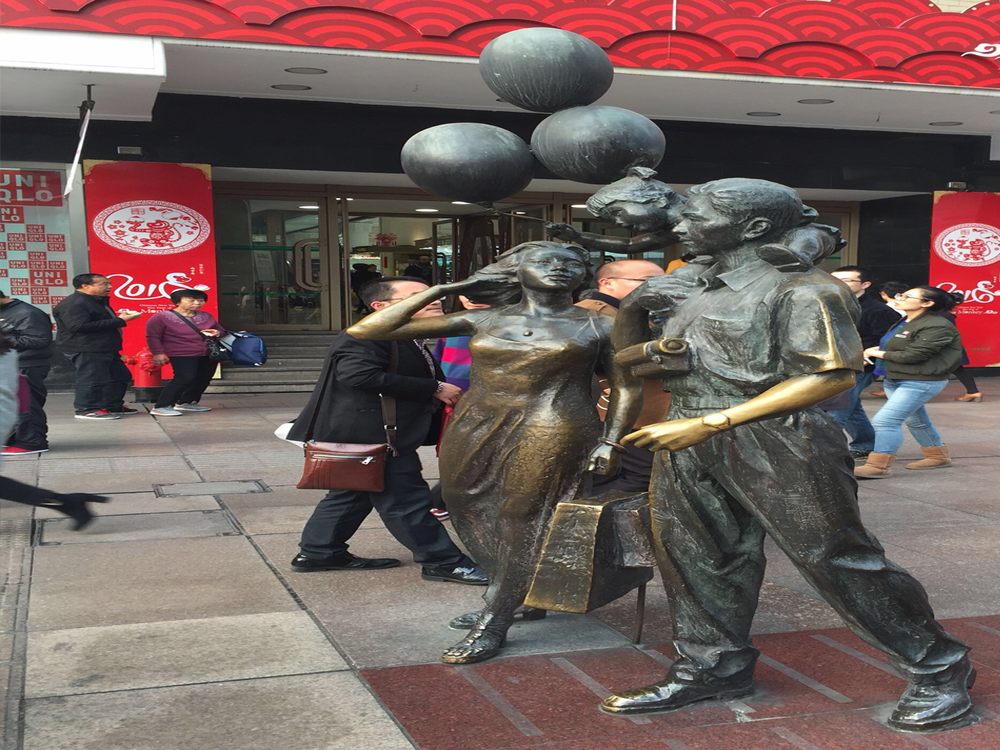
Creating porcelain sculptures with variable thickness is a delicate art that demands precision, creativity, and technical expertise. Artists and manufacturers face several challenges, including uneven drying, structural weakness, and cracking during firing. To address these issues, they employ a combination of traditional methods and modern innovations.
One key technique is controlled drying. Artists often work in stages, allowing thicker sections to dry slowly while thinner areas are monitored for premature hardening. This prevents warping and ensures uniformity. Additionally, some use specialized tools like ribbing tools or sponges to evenly distribute moisture during shaping.
Structural integrity is another critical concern. Reinforcing thicker areas with internal supports or armatures helps prevent collapse during firing. Some artists blend porcelain with additives like paper fiber or grog to enhance strength without compromising aesthetics.
Firing presents its own challenges. Kiln schedules are meticulously adjusted to accommodate variable thickness, with slower heating and cooling rates to minimize thermal stress. Advanced kilns with precise temperature control are often employed to ensure even heat distribution.
Manufacturers, on the other hand, leverage industrial techniques such as slip casting or 3D printing to achieve consistent results. These methods allow for precise control over wall thickness, reducing the risk of defects.
Ultimately, mastering variable thickness in porcelain sculptures requires a blend of artistic vision and technical skill. By embracing both time-honored traditions and cutting-edge technology, artists and manufacturers continue to push the boundaries of ceramic art.