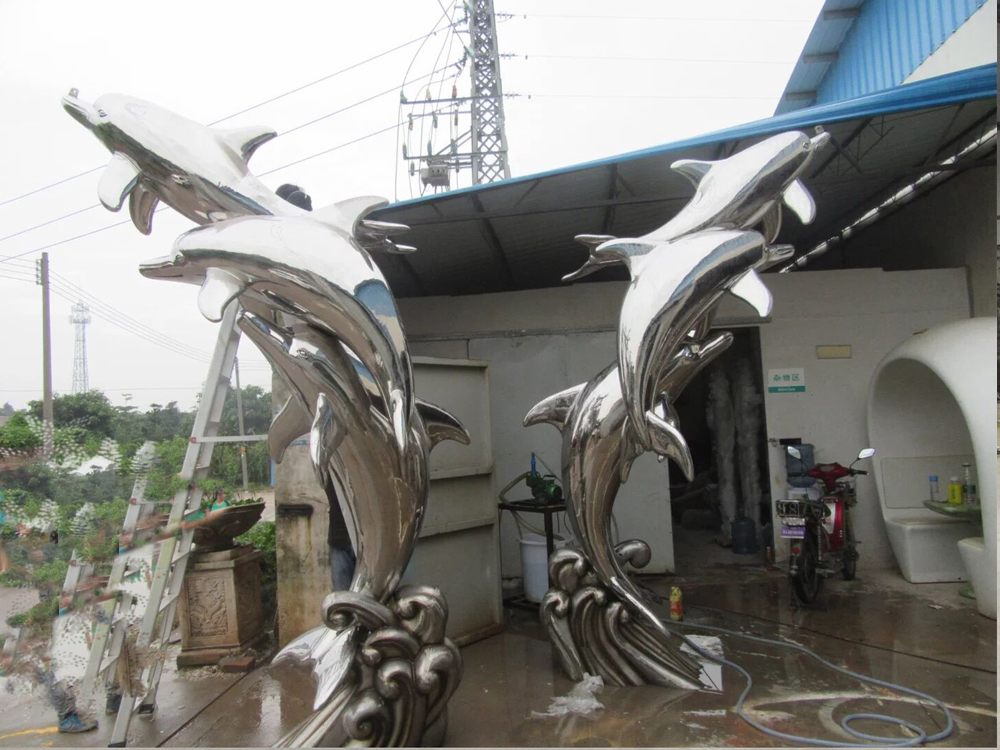
Creating layered or multi-component porcelain sculptures requires mastery of both artistic vision and technical ceramic skills. Artists typically begin by designing their sculpture in sections, considering how each component will interact structurally and aesthetically. The most common techniques include:
1. Slip Casting: Pouring liquid porcelain (slip) into plaster molds to create uniform components that can be assembled after drying.
2. Hand-Building: Using coils, slabs, or pinch methods to form organic shapes, often combined with carved details.
3. Multiple Firings: Components are often bisque-fired separately before assembly, with final glazing requiring precise temperature control to prevent warping.
4. Joinery Techniques: Scoring, slipping (applying liquid clay), and supporting structures ensure seamless bonding between layers.
5. Glazing Strategy: Artists may layer glazes or use wax resist to create depth, with some firing cycles exceeding 1,300°C for translucency.
The process demands patience—a single sculpture may take weeks to complete due to drying times and sequential firings. Contemporary artists often combine traditional methods with 3D-printed molds or mixed media for innovative results.