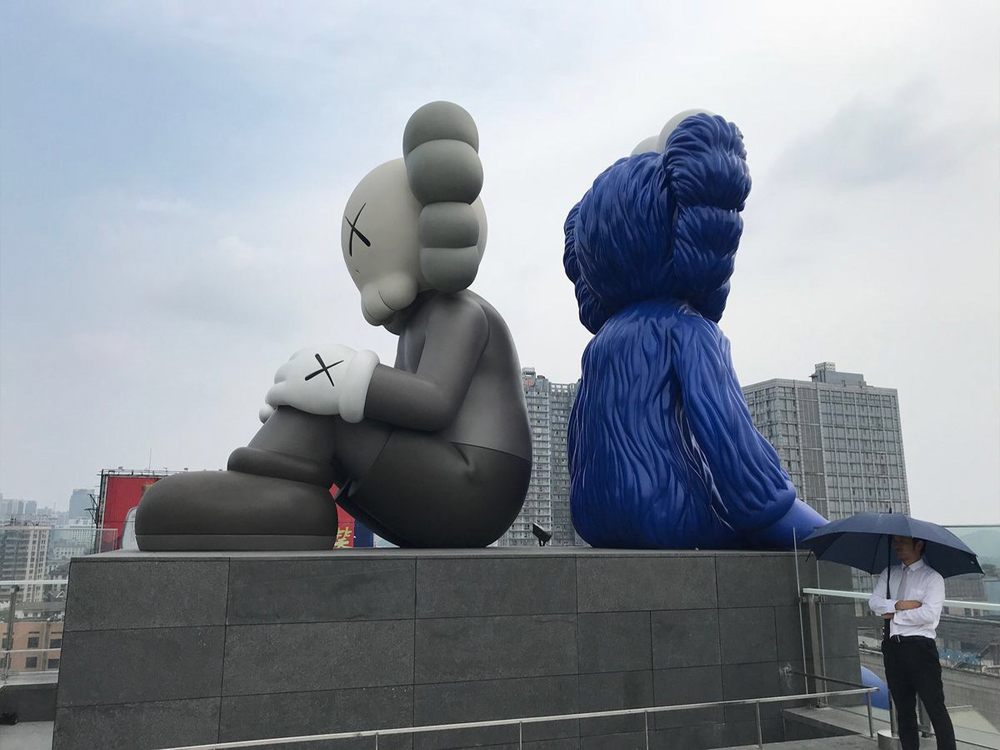
Creating hand-built porcelain sculptures with uniform thickness is essential for both aesthetic appeal and structural integrity. Uneven sections can lead to cracking or warping during drying and firing. Here are the most effective techniques to ensure consistency in your work:
1. Use Rolling Guides: When rolling clay slabs, place wooden or metal strips of equal thickness on either side of the clay. This ensures the rolling pin produces an even slab.
2. Measure with Calipers: Regularly check thickness using calipers or a needle tool. Mark problem areas and adjust pressure accordingly.
3. Maintain Consistent Clay Consistency: Wedge clay thoroughly to eliminate air pockets and ensure uniform density, which helps in even shaping.
4. Layer and Compress: For coil or slab construction, compress each layer firmly with a rib tool to eliminate variations and blend seams seamlessly.
5. Rotate and Flip: When hand-building, frequently rotate the piece to apply even pressure from all angles, preventing thin or thick spots.
6. Slow Drying: Cover the sculpture with plastic and dry it slowly to prevent uneven shrinkage, which can exaggerate thickness discrepancies.
By mastering these methods, artists can produce flawless porcelain sculptures with professional-level precision. Patience and attention to detail are key to achieving uniform results.