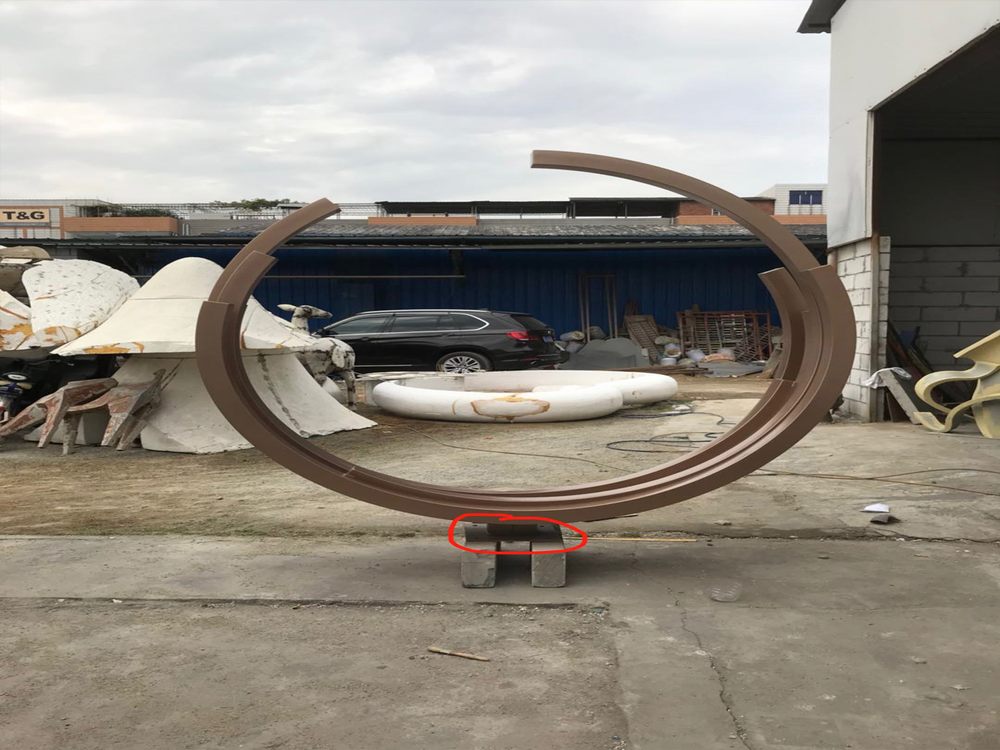
Artists face significant challenges when drying and firing ceramics, as improper techniques can lead to cracking or warping. To prevent these issues, professionals employ a combination of material knowledge and controlled processes.
During the drying phase, artists ensure even moisture evaporation by covering works with plastic or damp cloths to slow drying. They avoid direct heat or sunlight, which causes uneven shrinkage. Thicker pieces require longer drying times, often weeks, to prevent internal stress cracks.
For firing, artists use kiln schedules that gradually increase temperature, allowing residual moisture to escape safely. Bisque firing at lower temperatures (around 1800°F) before glaze firing helps strengthen the clay body. Strategic placement in the kiln prevents uneven heating, while proper clay selection (with appropriate grog content) reduces thermal shock risks.
Advanced techniques include compressing clay thoroughly when forming, using consistent wall thickness, and adding structural supports for large pieces. Many artists test new clay bodies and glazes with small samples before committing to major works. By mastering these methods, artists create durable ceramic pieces that withstand the stresses of drying and firing.