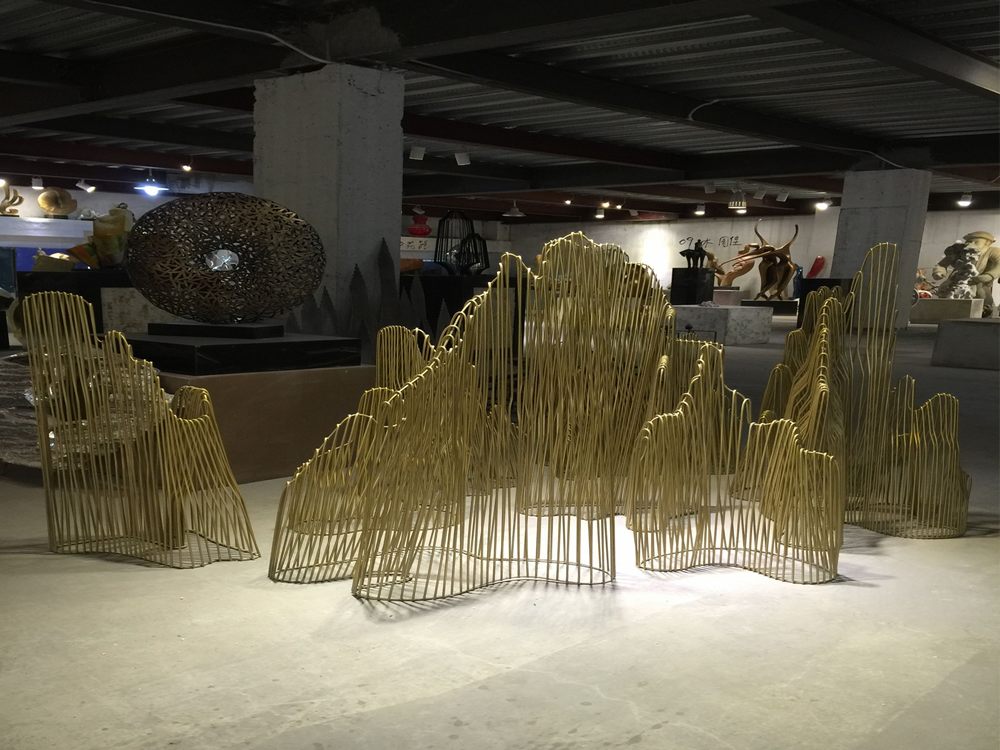
Creating porcelain sculptures with intricate detailing while preserving structural integrity is a delicate balance achieved through meticulous techniques and material expertise. Artists begin by selecting high-quality porcelain clay with optimal plasticity, allowing fine details to be carved without cracking. The process often involves working in stages—building a sturdy armature as a base, then adding thin layers of clay for delicate elements like lace or foliage.
To prevent warping, sculptors use controlled drying methods, such as covering sections with damp cloths or employing slow air circulation. Firing is another critical phase; low bisque firings stabilize the piece before higher-temperature glazing. Advanced artists may employ slip-casting for complex designs, pouring liquid clay into molds to capture fine textures.
Modern innovations like 3D-printed molds or laser-guided carving tools enable unprecedented precision, while traditionalists rely on hand tools like needles and ribs. The key lies in understanding clay’s limits—reinforcing stress points with internal supports or hollowing thick sections to ensure even drying. Through patience and mastery, porcelain artists transform fragility into enduring beauty.