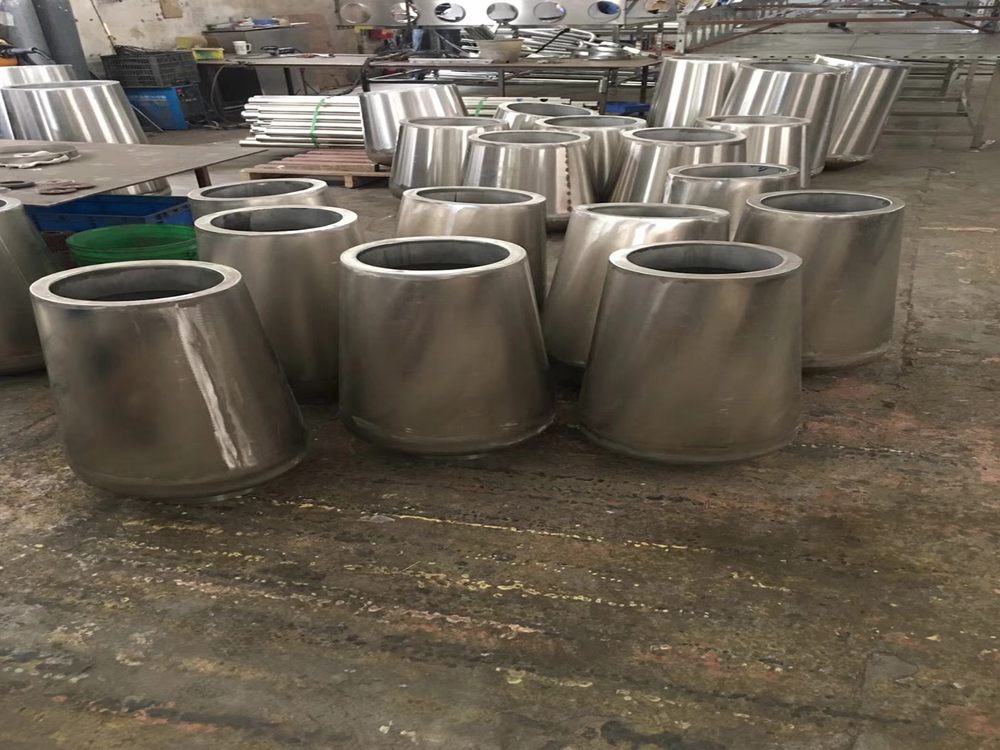
Creating large-scale porcelain sculptures is a delicate balance of artistry and engineering. Artists employ several techniques to ensure structural stability, starting with meticulous material selection. High-quality porcelain clay with balanced plasticity and strength is essential.
The design phase incorporates strategic weight distribution, often using hollow sections or internal armatures to reduce stress. Artists may layer the clay in stages, allowing each section to dry partially before adding more, preventing collapse.
Kiln firing is critical. Slow, controlled heating and cooling cycles minimize cracking, while advanced kilns with precise temperature regulation ensure even heat distribution. Some artists use multiple firings at varying temperatures to strengthen the piece incrementally.
Innovative techniques like slip casting or coil building provide additional stability. Post-firing, epoxy resins or hidden metal supports may reinforce fragile areas. Through these methods, artists transform fragile porcelain into enduring monumental artworks.