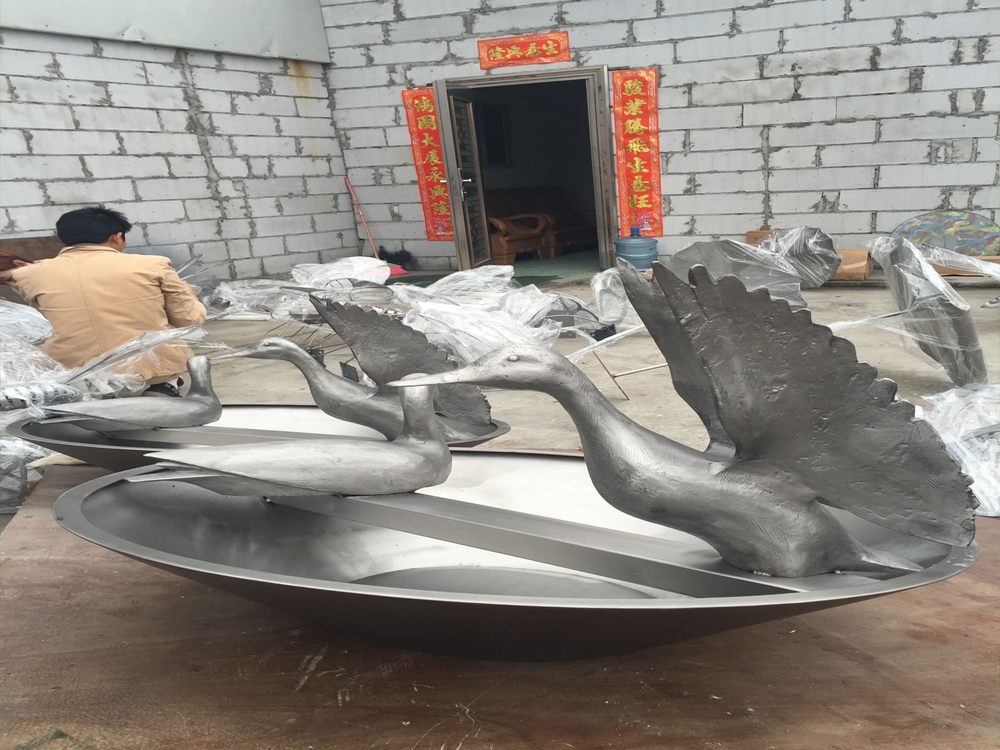
Creating porcelain sculptures with translucent layers requires a delicate balance of technical skill and artistic vision. The most common techniques include:
1. Thin-Wall Construction: Artists carefully build up extremely thin layers of porcelain (often just 1-2mm thick) through precise wheel-throwing or hand-building methods. This allows light to penetrate the material while maintaining structural integrity.
2. Slip Casting: Liquid porcelain (slip) is poured into plaster molds in multiple layers, with each layer allowed to partially dry before adding the next. This creates graded translucency when fired.
3. Lamination Technique: Thin sheets of porcelain are layered with slightly varied compositions, then fused together during firing to create depth and light diffusion effects.
4. Hollow Building: Sculptors create hollow forms with strategically placed openings that allow light to pass through the thin porcelain walls, enhancing the translucent quality.
5. Differential Firing: Different sections of the sculpture are fired at varying temperatures to achieve contrasting levels of translucency within a single piece.
Master artisans often combine these methods, sometimes incorporating colored porcelain slips between layers or using specialized kiln-firing schedules to achieve the perfect balance between strength and light transmission. The key lies in understanding porcelain's unique properties - its particle alignment during forming and its vitrification behavior at high temperatures. Contemporary artists are pushing these techniques further by experimenting with digital modeling and 3D printing to create complex layered structures impossible to achieve by hand alone.