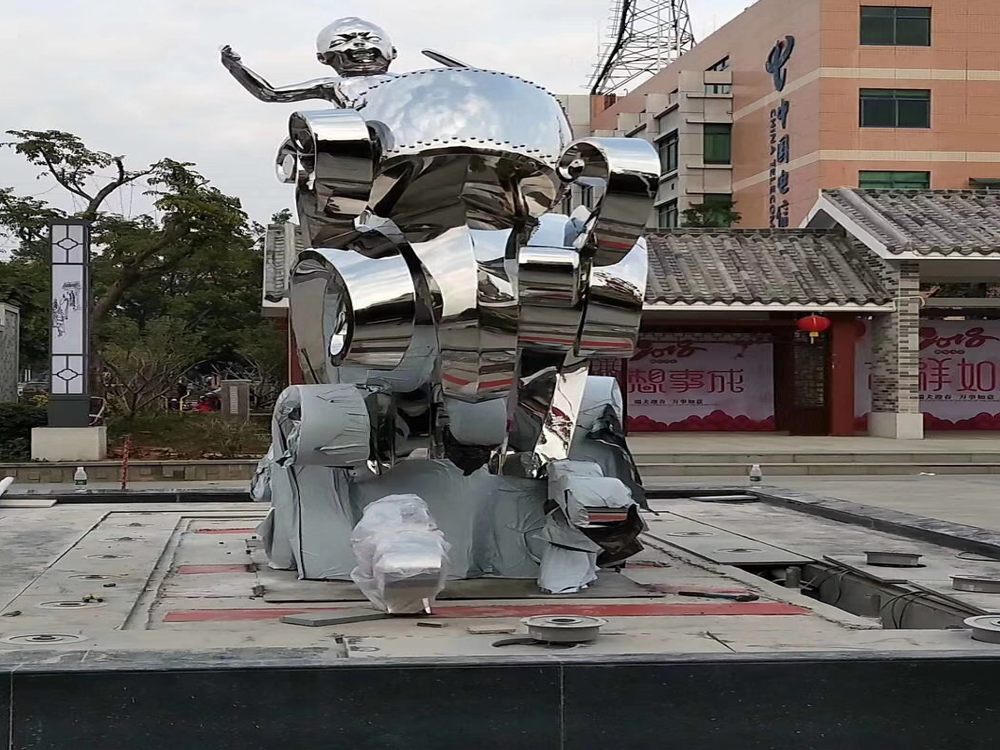
Creating porcelain sculptures with sound-responsive elements is a fascinating intersection of traditional craftsmanship and modern technology. Artists face unique challenges in merging fragile ceramic materials with functional auditory components, requiring innovative solutions at every stage.
The process begins with specialized clay formulations. Sculptors often blend porcelain with additives to enhance durability while maintaining acoustic sensitivity. Some incorporate conductive materials like silver or graphite into the glaze, allowing the piece to respond to vibrations.
Structural engineering proves critical. Hollow chambers are carefully designed within sculptures to amplify specific frequencies, while thin-walled sections vibrate like diaphragms. Japanese artist Yuri Kobayashi creates porcelain "singing vessels" with precisely calibrated thickness variations that produce harmonic tones when stroked.
Electronic integration presents another hurdle. Miniature contact microphones or piezoelectric sensors are embedded during firing, with wiring channels pre-planned in the clay body. The team at Studio ThusThat developed a method where gold circuits survive the kiln's extreme heat, creating sculptures that generate voltage when tapped.
Contemporary practitioners like Zimoun have pushed boundaries by combining industrial materials with porcelain. His installations feature hundreds of hand-thrown ceramic components activated by electromagnetic systems, creating immersive soundscapes that respond to viewer movement.
The final challenge lies in balancing aesthetic purity with functionality. As ceramicist Caroline Slotte explains: "The magic happens when the technology disappears, leaving only the poetic interaction between human, object, and sound." This delicate equilibrium continues to inspire new generations of artists working at the sonic frontier of porcelain art.