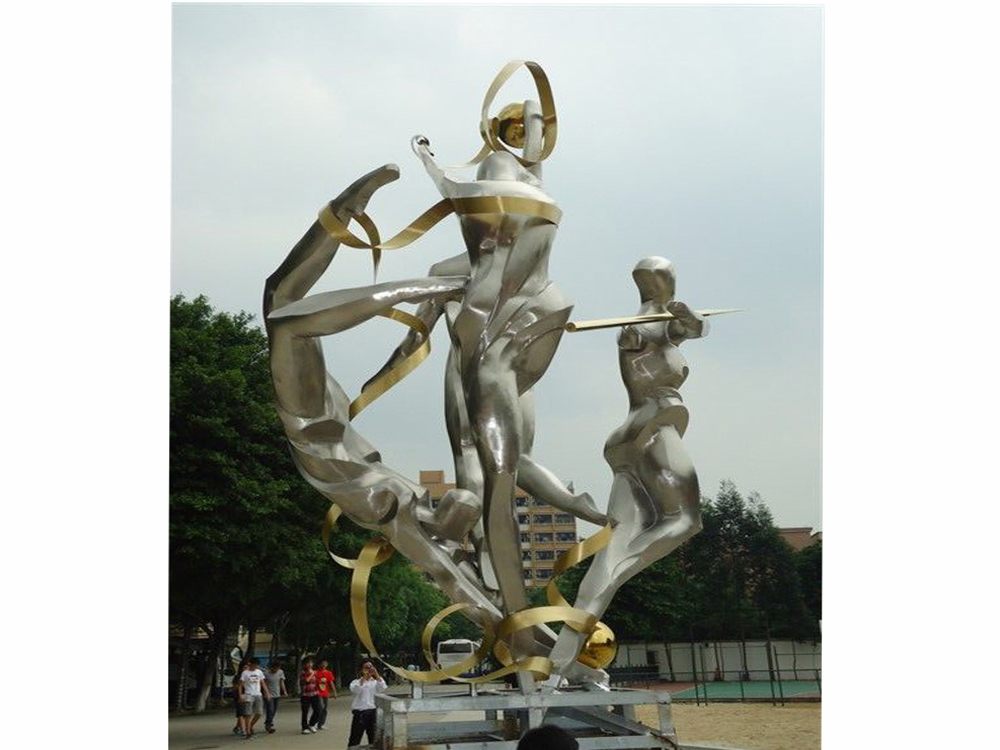
Creating porcelain sculptures for high-vibration environments presents unique challenges that test the limits of ceramic art. The fragility of porcelain, while prized for its delicate beauty, becomes a liability in settings with constant movement or mechanical stress. One major issue is material fatigue—repeated vibrations can cause microscopic cracks to propagate, leading to catastrophic failure over time. Artists must carefully consider wall thickness distribution, as uneven sections create weak points prone to fracturing.
Glaze compatibility poses another hurdle, as thermal expansion mismatches between clay body and glaze can accelerate cracking under vibrational stress. The sculpture's mounting system also requires special attention; traditional methods may transfer vibrations directly into the piece. Some artists incorporate vibration-dampening materials like silicone isolators into their displays.
Perhaps most challenging is achieving artistic expression while meeting structural demands. The elegant, thin forms prized in porcelain often conflict with the need for robust construction. Advanced techniques like slip-casting with reinforced clay bodies or post-firing treatments are emerging solutions, but these often compromise the material's pure ceramic qualities that make porcelain so desirable.
Successful pieces for these environments typically feature simplified geometries that distribute stress evenly, along with specialized firing protocols to maximize density. As demand grows for art in industrial and architectural settings, porcelain artists continue innovating to meet these demanding conditions without sacrificing aesthetic value.