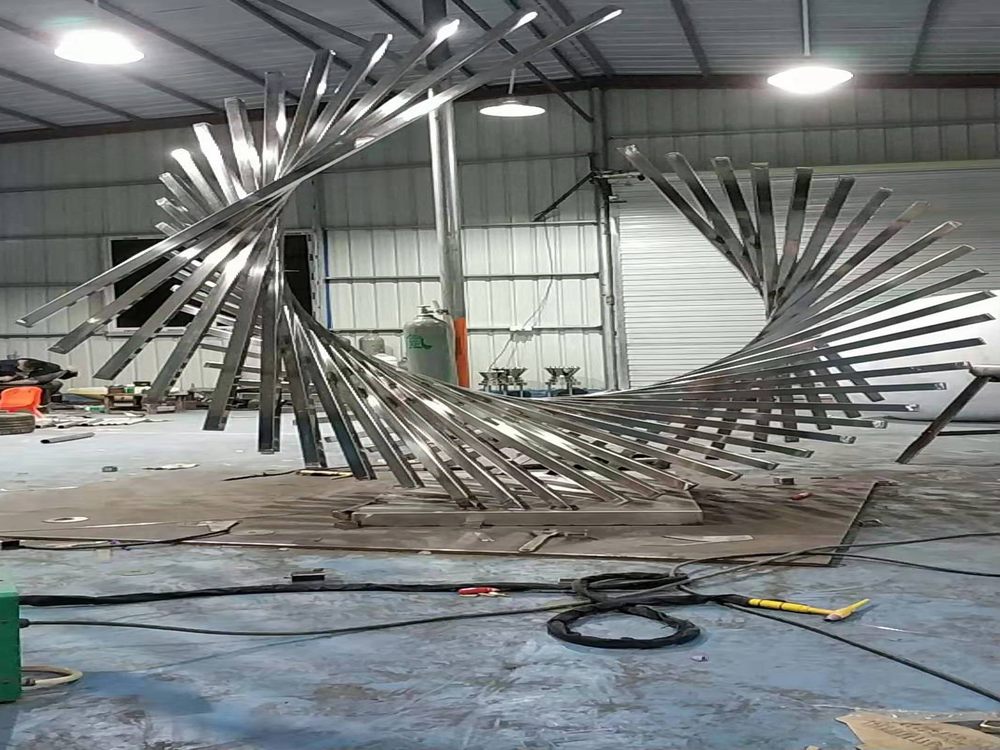
Creating porcelain sculptures with temperature-sensitive elements is a delicate art that demands both technical precision and creative ingenuity. Artists tackle this challenge through a combination of material science, kiln mastery, and innovative design approaches.
The process begins with careful clay selection, often blending porcelain with additives to improve thermal stability. Many artists use specialized low-fire porcelain or incorporate refractory materials that can withstand thermal stress. The sculpting phase requires anticipation of how different thicknesses will react to heat, with experienced artists creating uniform wall thicknesses to prevent cracking.
Kiln techniques prove crucial in the success of these works. Artists employ controlled cooling cycles, sometimes extending firing times over several days to gradually reduce temperature. Some utilize computerized kilns with precise programming capabilities, while others rely on traditional methods like saggars (protective ceramic boxes) to create microclimates around sensitive areas.
Innovative design solutions include creating sculptures in sections that are fired separately at optimal temperatures, then assembled post-firing with ceramic adhesives. Other artists embrace the unpredictability, incorporating intentional cracks or warping into their aesthetic. Contemporary practitioners are experimenting with new technologies like 3D-printed porcelain scaffolds that provide structural support during firing.
The most successful artists combine technical knowledge with artistic vision, viewing temperature sensitivity not as a limitation but as a creative partner in the artistic process. Through continuous experimentation and respect for the material's nature, they transform potential weaknesses into distinctive artistic strengths.