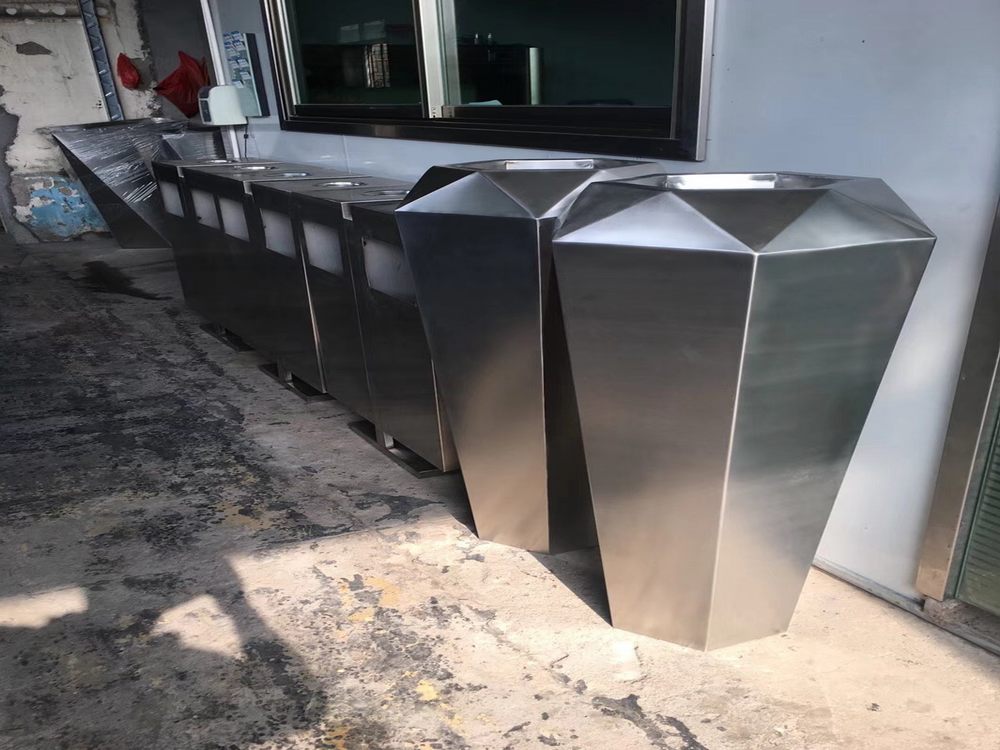
Creating large-scale porcelain sculptures presents unique artistic and technical challenges that test even the most experienced ceramic artists. The first major obstacle is porcelain's inherent fragility - this delicate material becomes increasingly vulnerable as size increases, requiring innovative structural support systems. Many artists incorporate hidden metal armatures or design self-supporting shapes to prevent collapse.
The drying process poses another significant challenge. Porcelain shrinks dramatically (up to 15%) during drying and firing, making large pieces prone to cracking. Artists must carefully control humidity and drying rates, sometimes taking months to properly dry a single sculpture before firing.
Kiln firing presents its own set of difficulties. Large sculptures often require custom-built kilns, and the high temperatures needed (typically 1300-1400°C) can cause warping or slumping. Some artists fire pieces in sections and assemble them afterward, adding complexity to the process.
Glazing large works requires exceptional skill, as uneven application can lead to cracking or color inconsistencies. Many sculptors develop specialized spraying techniques or apply multiple thin layers to achieve uniform coverage.
Finally, the weight of finished pieces creates logistical challenges for transportation and installation. Some monumental porcelain sculptures require custom crating and structural engineering for display. Despite these hurdles, artists continue pushing porcelain's boundaries, creating breathtaking large-scale works that showcase both the material's beauty and their technical mastery.