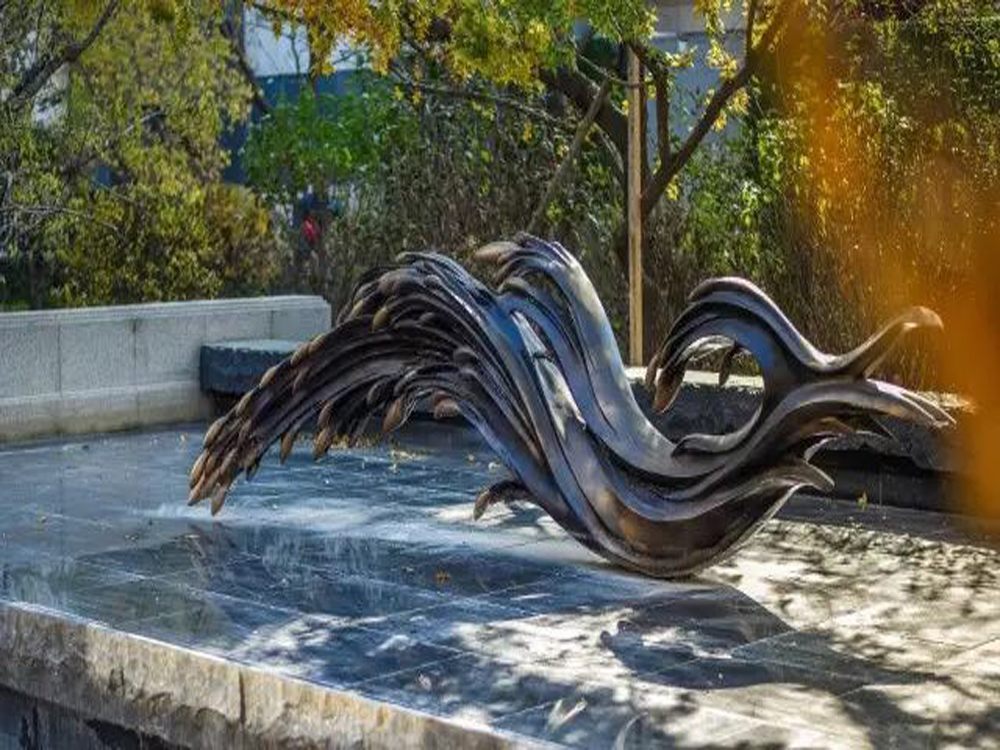
Creating custom porcelain sculptures with precise color matching is a complex process fraught with challenges. One major hurdle is material inconsistency; variations in clay composition and glaze formulas can lead to unexpected color shifts. Firing conditions also play a critical role, as even slight temperature fluctuations in the kiln can dramatically alter final hues.
Another common issue is the subjective nature of color perception. Clients may describe colors differently, and digital renderings often fail to accurately represent true ceramic tones. Additionally, glaze interactions create unpredictable results, with layered applications sometimes producing entirely new colors.
The aging process of porcelain adds another layer of complexity, as some glazes change color over time due to environmental factors. Master artisans must account for all these variables while maintaining artistic integrity, making precise color matching one of the most demanding aspects of custom porcelain work.
Solutions include maintaining strict material controls, conducting extensive test firings, and establishing clear communication protocols with clients. Advanced digital color matching systems are increasingly being adopted, though the human eye remains the ultimate judge in fine ceramic art.