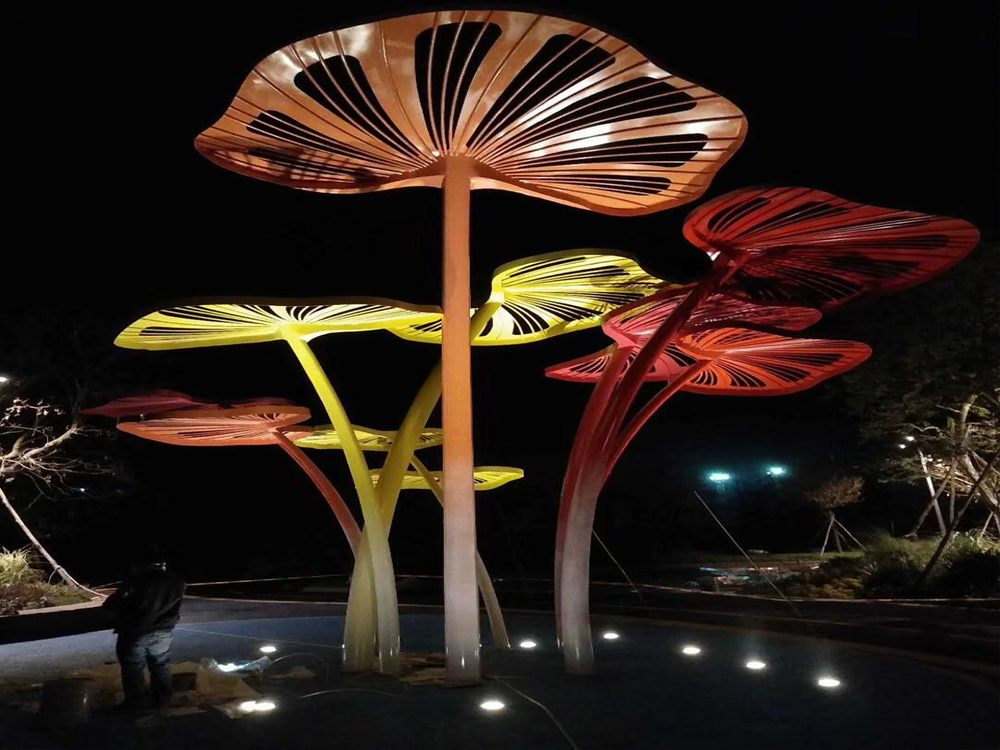
Artists meticulously address glaze fit to prevent cracking or flaking in ceramics by understanding the interplay between clay bodies and glaze compositions. The key lies in matching the thermal expansion rates of both materials—when clay and glaze expand and contract at similar rates during firing and cooling, stress is minimized. Experienced potters test glaze recipes on small tiles before full application, observing how they interact with specific clay types.
Controlled drying and firing cycles are critical; rapid temperature changes can exacerbate misfit issues. Many artists layer glazes strategically, using underglazes or slip to create a buffer between the clay and outer glaze. Some incorporate additives like silica or alumina to adjust glaze viscosity and adhesion. Modern ceramicists also leverage digital tools to calculate precise expansion coefficients, ensuring compatibility before even mixing materials.
The most skilled artisans view glaze fit as an ongoing dialogue between material science and artistic vision—balancing aesthetic goals with technical precision to create works that endure structurally while achieving desired visual effects. This fusion of creativity and chemistry separates functional pottery from fragile pieces destined to fail over time.