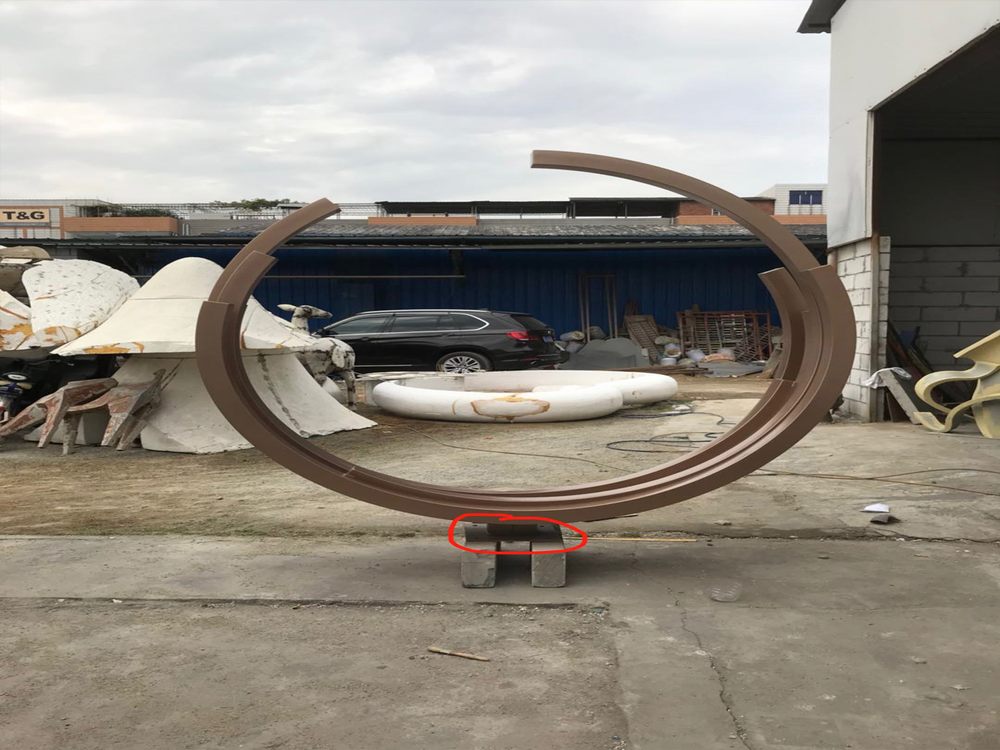
Creating multi-part porcelain sculptures is a delicate art that demands precision at every stage. One of the most common challenges is material shrinkage during drying and firing, which can cause misalignment between pieces. Porcelain clay contracts significantly, often requiring artists to pre-calculate shrinkage rates for accurate assembly.
Another hurdle is achieving seamless joins between sections. Even minor inconsistencies in thickness or curvature can lead to visible gaps or weak bonds. Skilled sculptors often use scoring, slip application, and careful compression to ensure strong adhesion.
Thermal stress during kiln firing also poses difficulties. Different sections may heat or cool at varying rates, increasing the risk of cracks or warping. Artists combat this by controlling firing cycles and sometimes assembling pieces post-firing.
The complexity increases with intricate designs featuring interlocking components. Each connection point becomes a potential failure spot, demanding meticulous planning from the initial design phase through final glazing.
Lastly, the fragile nature of unfired porcelain makes handling multi-part sculptures particularly challenging. Supporting structures and careful transportation methods are often necessary to prevent damage before firing.
Mastering these challenges requires both technical knowledge and artistic intuition, making flawless multi-part porcelain sculptures true testaments to a ceramic artist's skill.