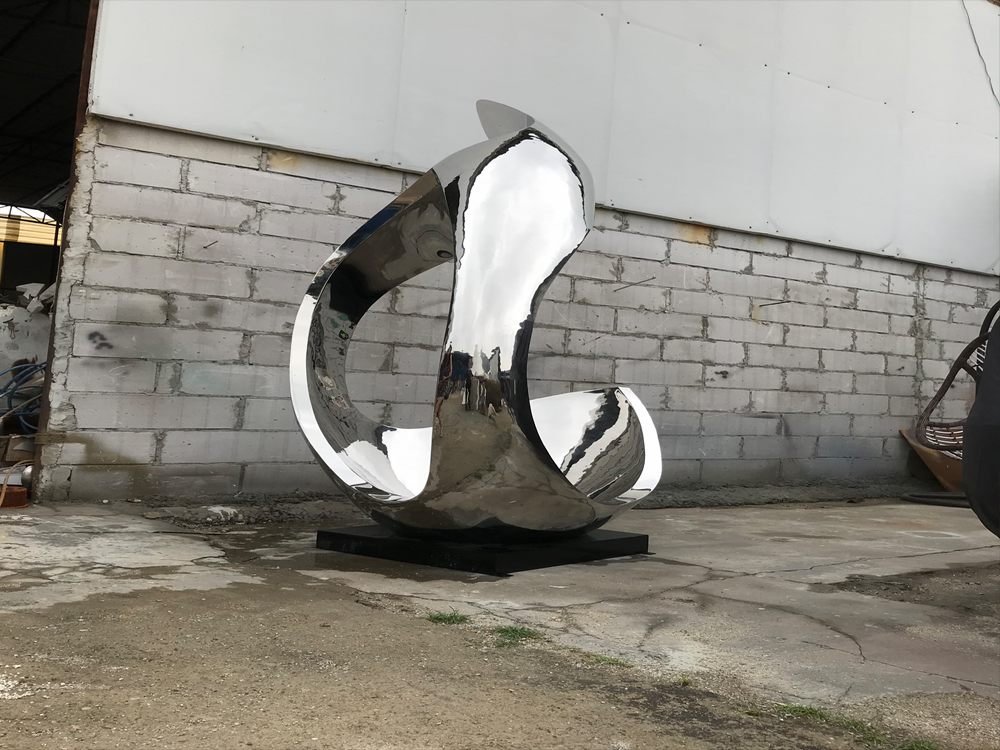
Creating large-scale porcelain sculptures is a demanding art form that combines technical precision with creative vision. Artists and ceramicists often face several significant challenges throughout the process.
1. Material Fragility: Porcelain is notoriously delicate, especially when scaled up. The risk of cracking or collapsing during shaping, drying, or firing increases with size, requiring meticulous handling and support structures.
2. Structural Integrity: Ensuring stability in large pieces demands careful engineering. Internal armatures or supports are often necessary, but these must account for porcelain’s shrinkage during firing, which can lead to warping or breakage.
3. Kiln Firing Limitations: Firing large sculptures requires specialized kilns with sufficient space and even heat distribution. Uneven temperatures can cause fractures, while prolonged firing cycles heighten the risk of defects.
4. Weight Management: As size increases, so does weight. Transporting and installing heavy porcelain sculptures without damage poses logistical challenges, often requiring custom solutions.
5. Glazing Consistency: Achieving uniform glaze application on large surfaces is difficult. Variations in thickness or drying rates can result in uneven finishes or cracks.
6. Cost and Time: Large-scale porcelain work is resource-intensive. Extended drying times, multiple firings, and material waste contribute to high costs and lengthy production timelines.
Despite these hurdles, artists continue to push boundaries, developing innovative techniques like slip-casting, modular construction, or hybrid materials to overcome these obstacles. The result is breathtaking art that showcases porcelain’s ethereal beauty on a monumental scale.