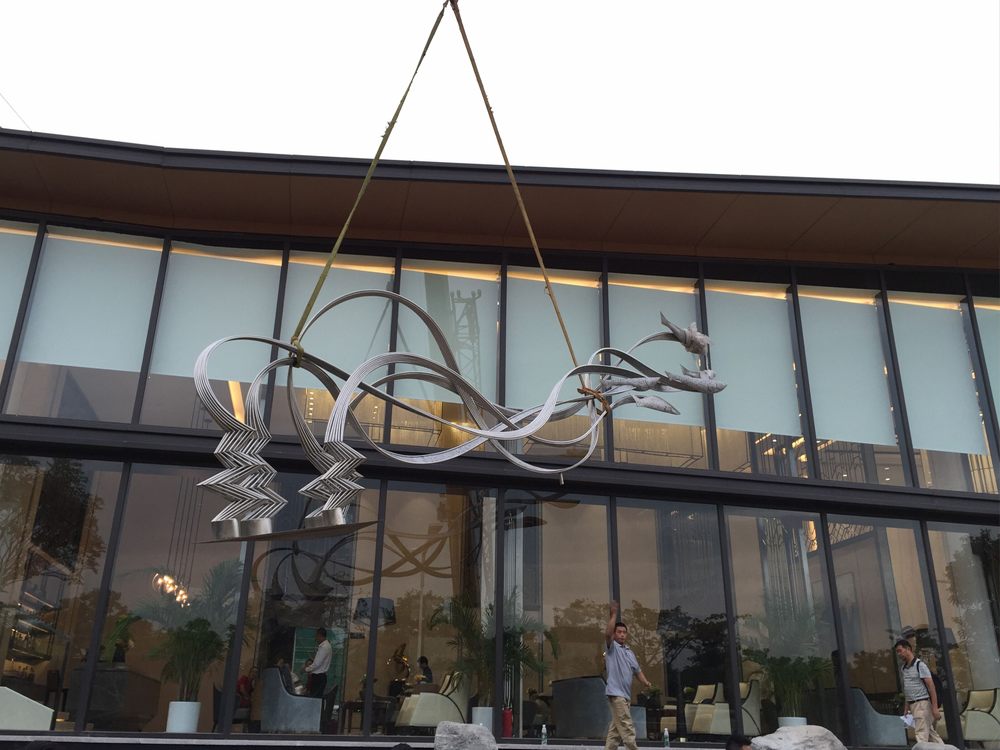
The durability of porcelain sculptures depends on multiple interconnected factors that art collectors and creators should understand. First, the quality of raw materials is fundamental - high-grade kaolin clay with proper mineral composition creates stronger molecular bonds during firing. Second, the firing temperature plays a crucial role; authentic porcelain requires at least 1,300°C to achieve optimal vitrification and density. Third, glaze formulation and application significantly impact resistance to environmental factors - properly formulated glazes create an impermeable surface barrier. Fourth, structural design affects longevity; balanced weight distribution and adequate thickness prevent stress fractures. Finally, the artist's technique in joining components and controlling cooling rates determines internal stability. Professional conservators emphasize that even seemingly minor variations in any of these factors can dramatically affect a sculpture's ability to withstand temperature changes, humidity fluctuations, and physical stress over decades. Understanding these elements helps collectors make informed acquisitions and enables artists to create works destined for permanence.