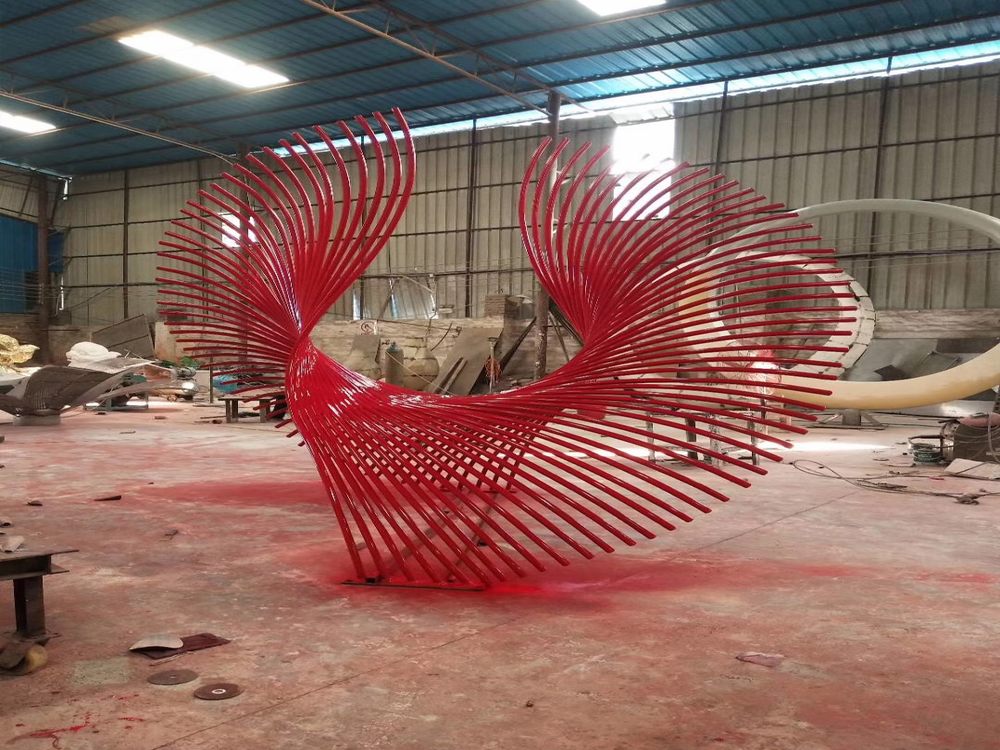
Creating hollow porcelain sculptures that retain structural integrity is a delicate balance of artistry and engineering. Artists achieve this through several specialized techniques. First, they carefully design the sculpture's form, ensuring even wall thickness (typically 3-5mm) to prevent cracking during drying and firing. Many use coil-building or slab construction methods, gradually building up layers while maintaining consistent density.
The clay composition itself is crucial - porcelain artists often mix their clay with grog (pre-fired ceramic particles) or paper fibers to improve tensile strength. Strategic placement of internal supports and ribs within the hollow form helps distribute structural loads. During drying, controlled humidity prevents uneven shrinkage.
The firing process is equally critical. Artists employ slow bisque firing (up to 1000°C) to thoroughly remove moisture before the final high-temperature firing (1280-1400°C). Some use multiple firing cycles with glaze applications to reinforce the surface. Modern artists sometimes incorporate 3D-printed porcelain supports that burn out during firing, leaving perfect hollow structures.
Master ceramicists also utilize compression techniques - carefully compressing the clay particles during forming creates molecular alignment that enhances strength. The finished hollow sculptures often prove surprisingly durable, as the uniform stress distribution in a properly designed hollow form can actually outperform solid pieces of similar size.