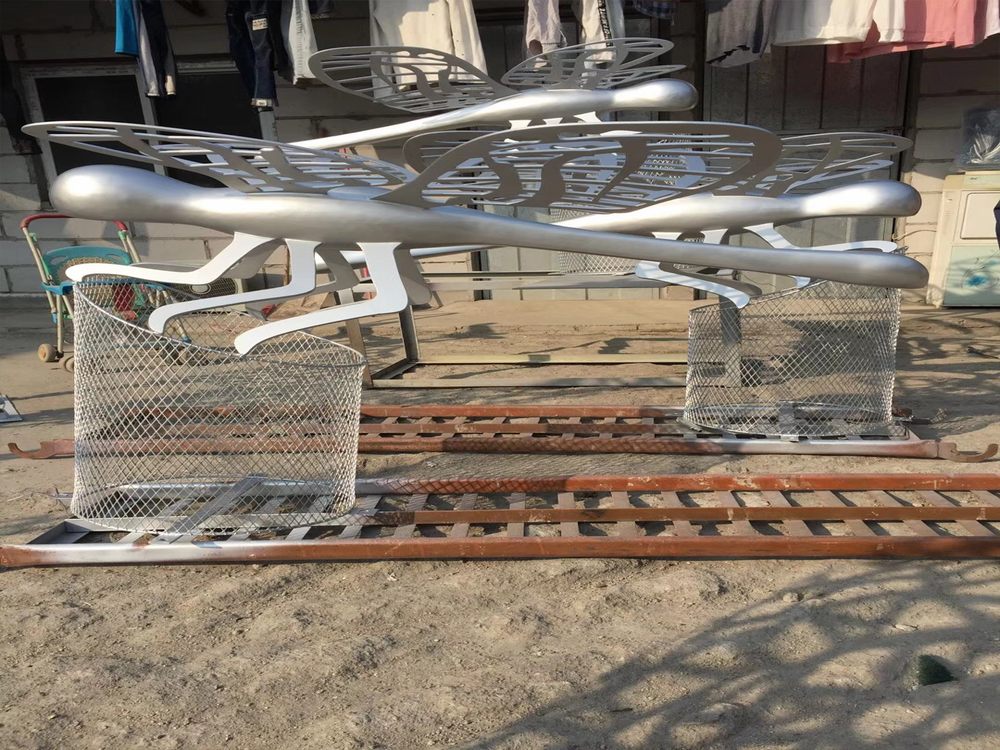
Creating porcelain sculptures with extreme scale variations presents unique challenges for artists and ceramicists. One major issue is structural integrity—larger pieces require careful engineering to prevent collapse during shaping and firing, while miniature details demand precision tools and steady hands. Firing inconsistencies also arise, as thicker sections may retain moisture longer, leading to cracks or warping. Glazing becomes complex when scaling up or down, as color reactions and surface textures behave differently. Additionally, clay composition must be adjusted to accommodate varying thicknesses, balancing plasticity and strength. Transporting and installing large-scale porcelain works adds logistical hurdles, whereas tiny sculptures risk fragility during handling. Mastering these challenges requires technical expertise and creative problem-solving to achieve harmonious results across vastly different sizes.