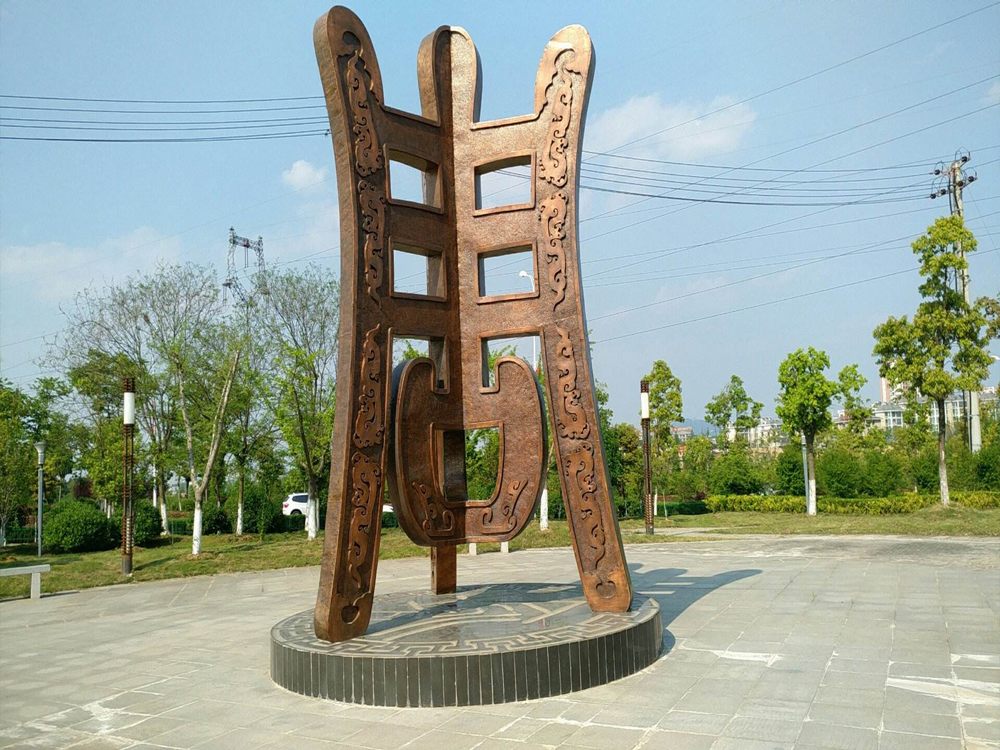
Creating porcelain sculptures with embedded or inlaid materials presents a unique set of challenges that test the limits of ceramic artistry. One primary difficulty lies in material compatibility. Porcelain and embedded materials like metals, glass, or stones often have different thermal expansion rates, leading to cracks or warping during firing. Artists must carefully select materials that can withstand the high temperatures of a kiln without compromising structural integrity.
Another challenge is the precision required during the inlaying process. Porcelain's delicate nature demands meticulous handling to avoid breakage while embedding foreign elements. The timing of insertion is critical—some materials are added before firing, while others are embedded post-firing, requiring specialized adhesives or techniques.
Firing techniques also pose significant hurdles. The kiln's temperature and cooling rate must be meticulously controlled to prevent thermal shock, which can cause the porcelain or embedded materials to fracture. Additionally, achieving a seamless aesthetic integration between porcelain and inlaid elements often requires multiple test firings to perfect the final appearance.
Finally, the artistic vision must balance practicality. While intricate designs with embedded materials can elevate a sculpture's beauty, the technical constraints may limit creative expression. Mastering these challenges, however, results in breathtaking works that showcase the harmony of diverse materials in porcelain art.