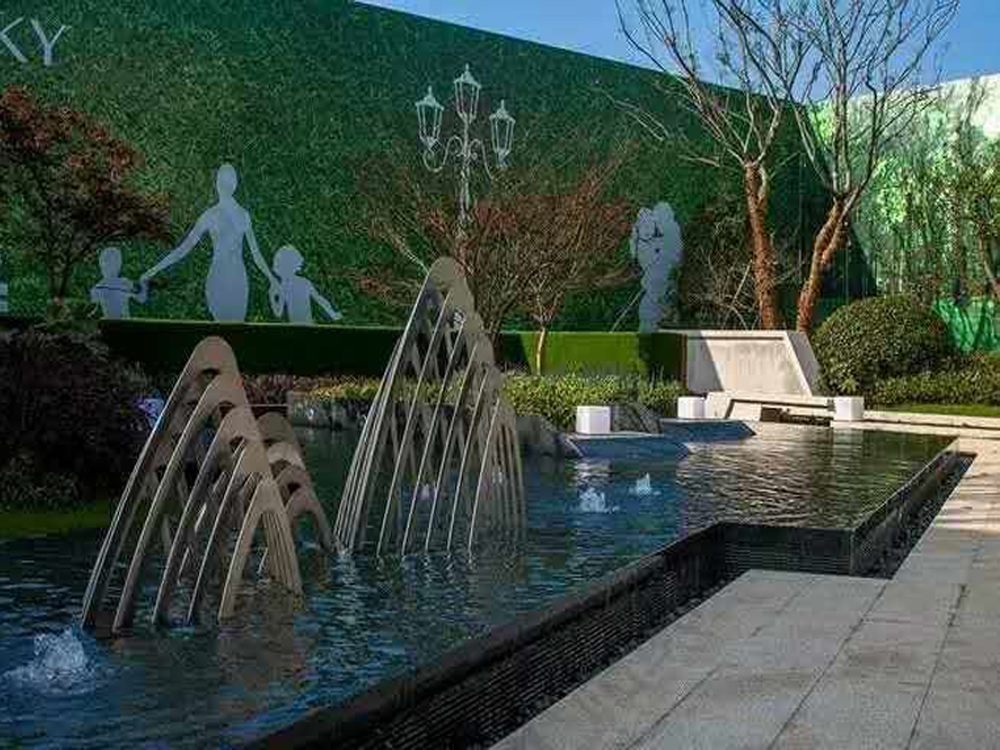
Creating porcelain sculptures with interchangeable parts is a delicate and complex art form that demands exceptional skill and precision. One of the primary challenges lies in the fragility of porcelain itself. This material, while prized for its luminous beauty, is highly susceptible to cracking or breaking during the sculpting and assembly processes. Artists must meticulously design each component to ensure seamless integration without compromising structural integrity.
Another significant hurdle is achieving consistent shrinkage rates during firing. Porcelain shrinks unpredictably in the kiln, which can render carefully crafted parts incompatible. Sculptors often rely on precise calculations and multiple test firings to mitigate this issue.
The engineering of joints and connectors presents yet another obstacle. These mechanisms must be discreet yet functional, allowing parts to be interchanged without visible seams or instability. Balancing aesthetics with practicality requires innovative solutions, such as hidden magnets or custom-designed grooves.
Finally, the glazing process adds complexity. Different sections may require varied glaze treatments, but overlapping applications can lead to undesirable interactions during firing. Mastering these challenges elevates porcelain sculpture into a realm where artistry and technical prowess intersect beautifully.