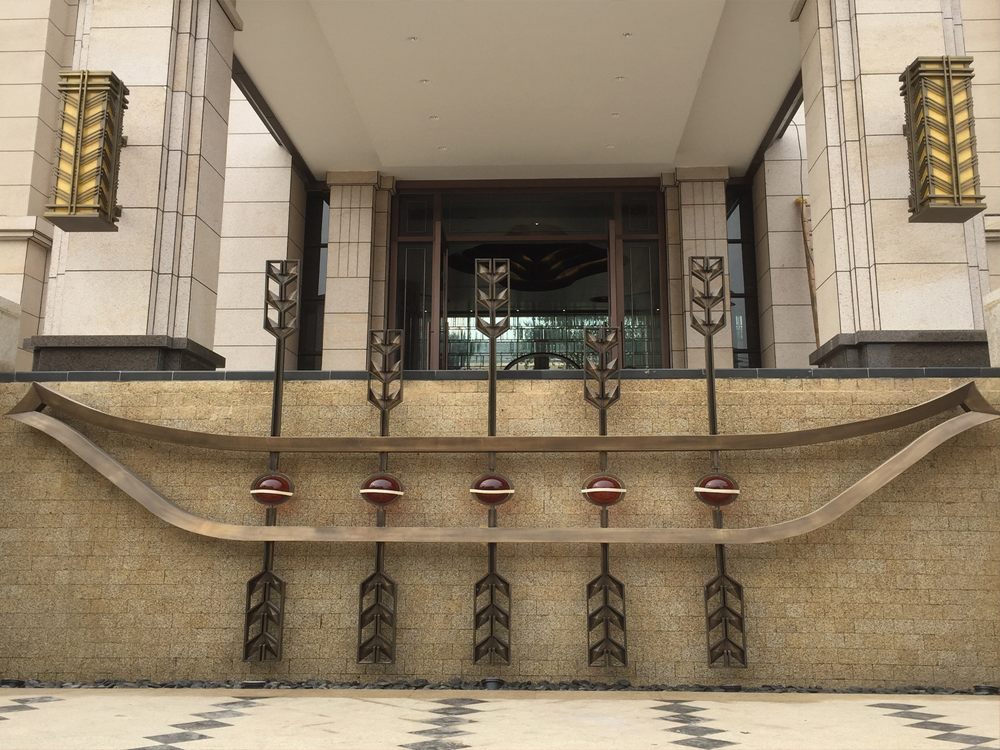
Porcelain sculptures have long been revered for their delicate beauty and intricate craftsmanship, rooted in centuries-old traditions. However, the advent of digital fabrication methods has introduced a transformative intersection between heritage techniques and modern technology.
Traditional porcelain sculpting relies on hand-molding, wheel-throwing, and kiln-firing—processes passed down through generations. These methods emphasize the artisan’s skill and tactile connection to the material. In contrast, digital fabrication, such as 3D printing and CNC milling, allows for precision and complexity unattainable by hand alone. Artists now use 3D modeling software to design intricate forms, which are then printed in porcelain or used to create molds for traditional casting.
This fusion preserves the authenticity of ceramic art while expanding creative possibilities. For instance, digital tools enable the replication of historic patterns with flawless accuracy or the experimentation with avant-garde geometries. Meanwhile, the final touch—glazing and firing—often remains in the hands of skilled craftsmen, ensuring the soul of traditional artistry endures.
The result is a dynamic dialogue between old and new, where porcelain sculptures become a canvas for innovation without losing their cultural essence. This synergy not only revitalizes the craft but also attracts a new generation of artists and collectors, ensuring its relevance in the digital age.