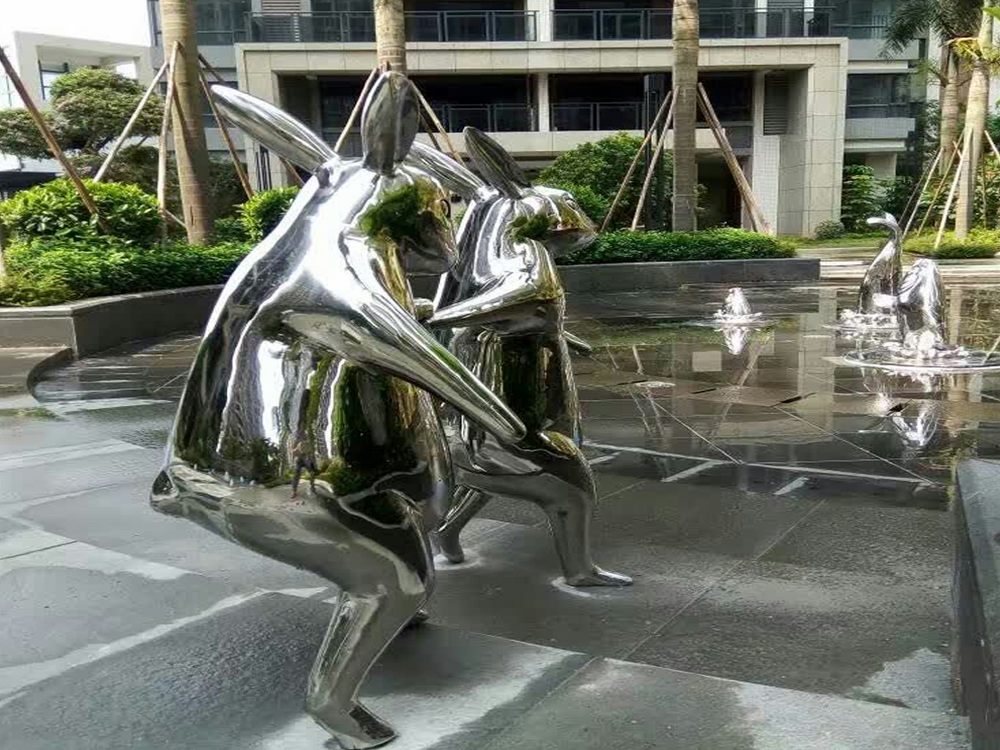
Glaze runoff and pooling are common challenges in porcelain sculpture creation, but artists and manufacturers employ a range of specialized techniques to achieve perfect results. The key lies in understanding the delicate balance between material science and artistic vision.
Experienced ceramicists begin by carefully formulating glaze viscosity. Adding materials like kaolin or bentonite increases thickness, preventing unwanted flow while maintaining vibrant colors. Many artists perform test firings with small sample tiles to observe how specific glaze combinations behave at different temperatures.
Kiln mastery forms the foundation of glaze control. Professionals program precise firing schedules, often including a "soak" period at critical temperatures to allow even distribution. Some studios use computerized kilns with multiple thermocouples to monitor heat variations throughout the chamber.
Innovative application methods also play a crucial role. Artists may apply multiple thin layers rather than single thick coatings, or use wax resist techniques to create barriers that stop glaze migration. Some sculptors employ the "dry foot" method, leaving the base unglazed to prevent sticking to kiln shelves.
Manufacturers have developed advanced solutions like engineered glazes with tailored flow characteristics. Certain commercial glazes contain additives that promote even distribution while minimizing drips. The ceramics industry continues researching nano-material solutions that could revolutionize glaze behavior.
Ultimately, preventing glaze defects requires both technical knowledge and artistic intuition. Mastering these methods allows creators to produce stunning porcelain works where the glaze enhances rather than compromises their sculptural vision. The interplay between controlled chemistry and creative expression remains at the heart of exceptional ceramic art.