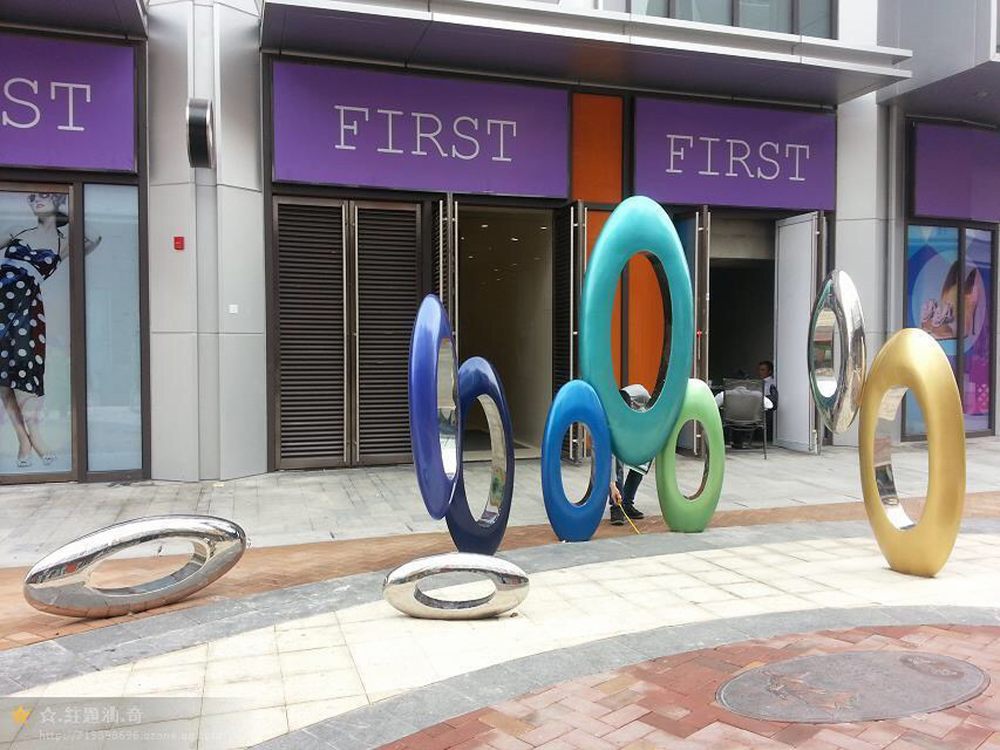
Creating a mold for a bronze sculpture is a meticulous process that requires precision and expertise. The most common and effective methods include the lost wax casting, sand casting, and ceramic shell techniques.
1. Lost Wax Casting: This ancient method involves sculpting the original model in wax, coating it with a refractory material, and then melting the wax away to leave a hollow mold. Molten bronze is poured into the cavity, resulting in a highly detailed sculpture.
2. Sand Casting: Ideal for larger sculptures, this technique uses compacted sand to form the mold. A pattern is pressed into the sand, removed, and bronze is poured into the impression. While less detailed than lost wax, it’s cost-effective for big projects.
3. Ceramic Shell Mold: A modern approach where the wax model is dipped in ceramic slurry and stucco repeatedly to build a strong, heat-resistant shell. After burnout, bronze is poured into the mold, yielding fine details and smooth surfaces.
Each method has its advantages, so choose based on your sculpture’s size, complexity, and budget. Proper mold-making ensures the longevity and beauty of your bronze artwork.