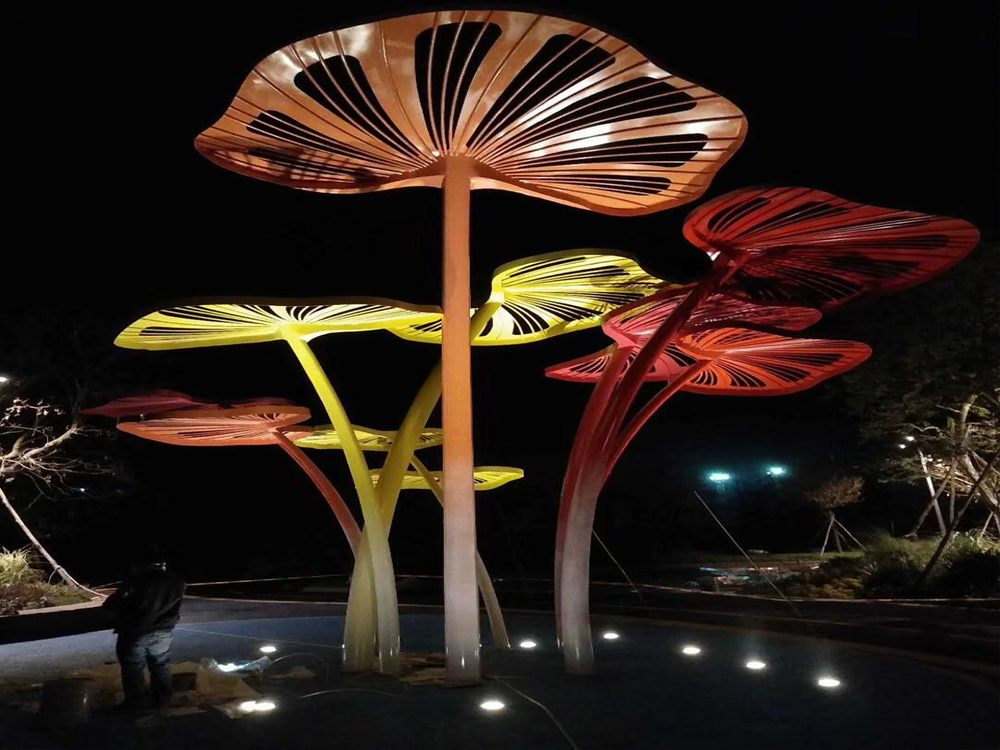
Bronze sculpture creation is a meticulous process that requires specialized tools at every stage. For the initial modeling phase, sculptors rely on clay tools like wire loops, ribs, and wooden modeling sticks to shape their designs. Once the clay model is complete, a variety of chisels, rasps, and files are used for refining details in the plaster or wax positive.
The metalworking phase demands heavy-duty equipment such as crucibles for melting bronze (typically heated to 1,100°C) and tongs for handling molten metal. Foundry tools like investment molds, ceramic shells, and centrifugal casting machines transform the wax model into bronze.
Finishing requires entirely different implements - from welding torches for assembling large pieces to patina brushes and chemical solutions for creating the characteristic bronze coloration. Many sculptors also use pneumatic tools like air scribes for texturing and angle grinders for polishing.
Modern digital tools have joined traditional implements, with 3D printers creating precise wax models and CNC routers assisting in large-scale works. However, the sculptor's most vital tools remain their hands and artistic vision - technology simply enhances age-old bronze-working techniques that date back millennia.