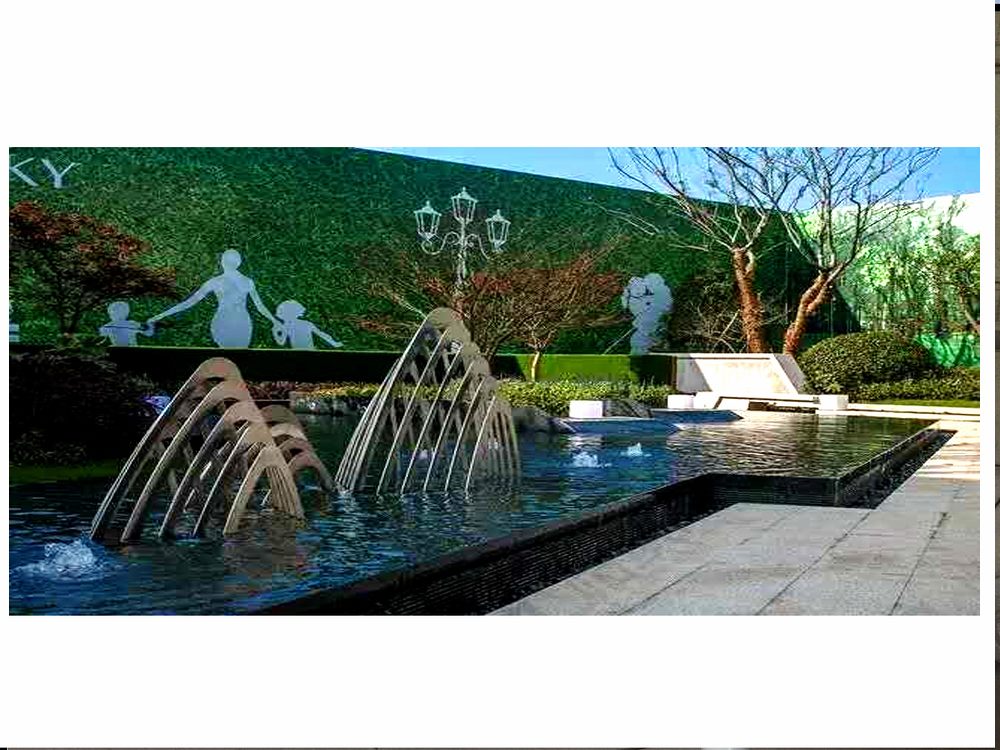
Bronze sculpture installation has evolved significantly over time, blending ancient techniques with contemporary innovations. Traditional methods relied heavily on manual craftsmanship, where sculptures were typically cast in single pieces or large sections using the lost-wax technique. Installation often involved simple pedestals or architectural integration, requiring physical strength and artisanal joinery skills.
Modern approaches incorporate advanced technologies like 3D modeling, modular casting, and precision engineering. Contemporary installations frequently use segmented construction with hidden internal support systems, allowing for more complex designs and larger scales. Modern methods also employ non-invasive anchoring systems, corrosion-resistant alloys, and sometimes even kinetic elements impossible in traditional works.
The most striking difference lies in precision and scalability. While traditional installations demanded perfect craftsmanship from the start, modern techniques allow for adjustments during assembly. Digital tools enable artists to visualize installations beforehand, reducing on-site challenges. However, many artists today intentionally combine both approaches, preserving traditional bronze patination methods while utilizing modern structural engineering for ambitious public art projects.
Environmental considerations also separate the eras. Traditional installations used lead-based solders and simple protective coatings, while modern methods employ eco-friendly alloys and advanced protective systems for outdoor durability. The choice between methods now often depends on artistic intent, with traditional techniques favored for authenticity and modern methods chosen for technical ambitiousness.