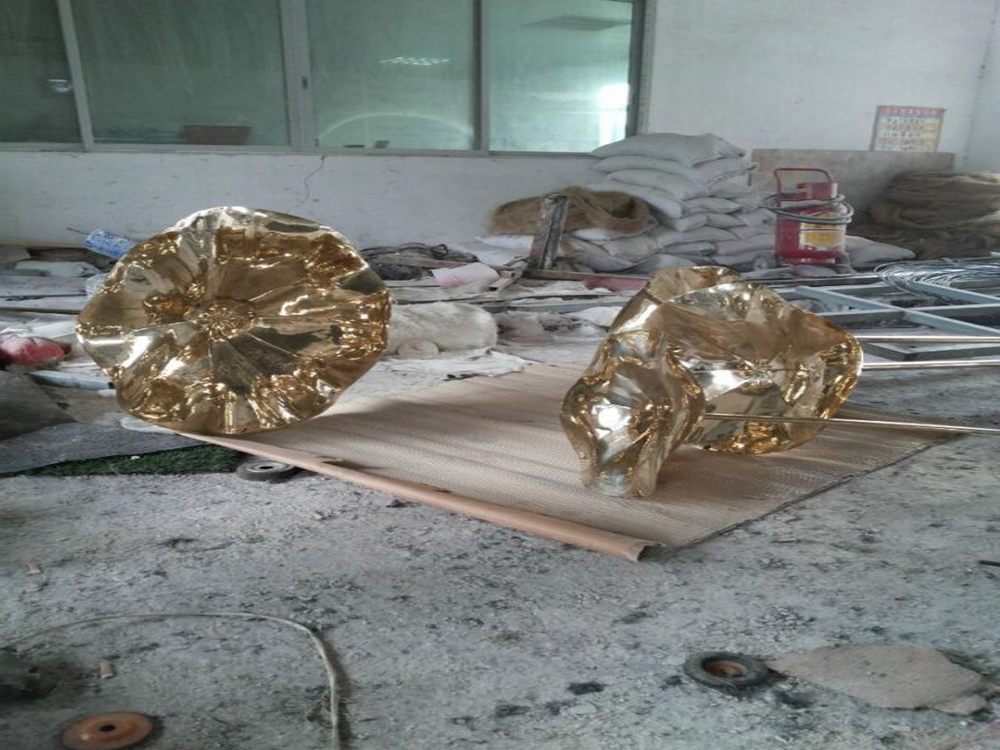
Intergranular corrosion in high-zinc bronze alloys is a critical issue that compromises structural integrity and longevity. To mitigate this, several proven strategies can be employed.
1. Alloy Stabilization: Adding small amounts of elements like nickel or tin helps stabilize the microstructure, reducing zinc segregation at grain boundaries.
2. Controlled Cooling Rates: Slow cooling during manufacturing minimizes thermal stress and prevents uneven zinc distribution, a primary cause of intergranular corrosion.
3. Heat Treatment: Solution annealing followed by rapid quenching homogenizes the alloy, dispersing zinc evenly and reducing corrosion susceptibility.
4. Protective Coatings: Applying corrosion-resistant coatings, such as ceramic or polymer layers, shields the alloy from environmental exposure.
5. Environmental Control: Limiting exposure to chlorides, sulfides, and acidic conditions significantly slows corrosion progression.
By combining these methods, manufacturers can enhance the durability of high-zinc bronze alloys in demanding applications.