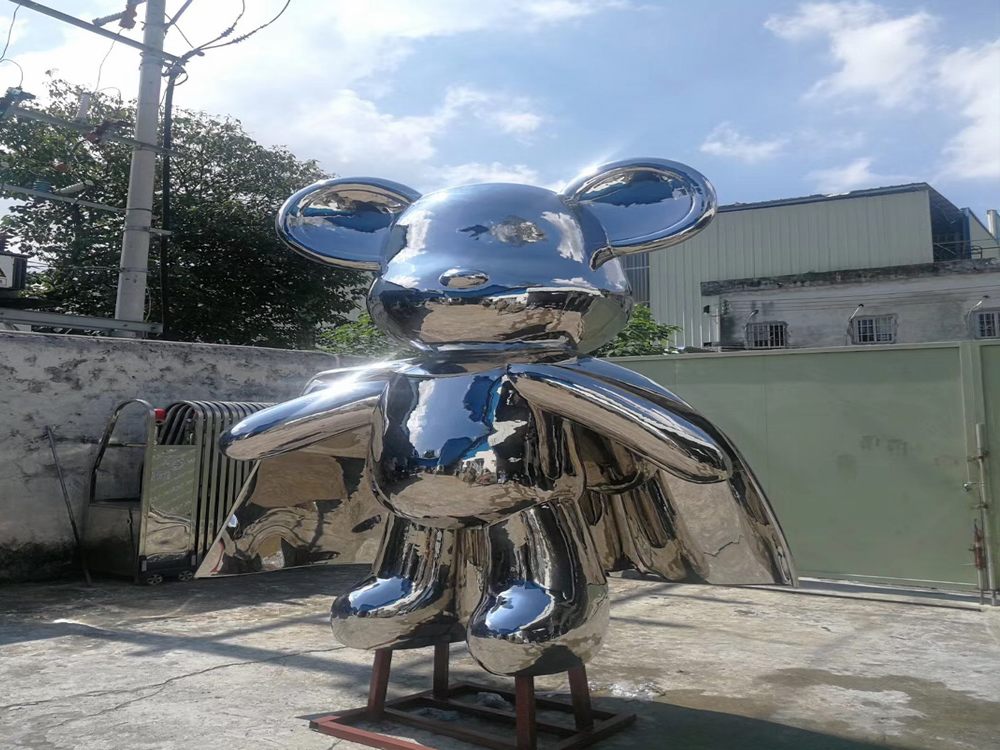
The finishing stages of bronze sculpture production are where the artwork truly comes to life, transforming raw metal into a visually stunning masterpiece. Artists rely on specialized tools and techniques to achieve the desired aesthetic and protective qualities in their bronze creations.
One of the most critical processes is patina application, which creates the distinctive coloration of bronze sculptures. Artists use heat torches to warm the metal surface before applying chemical solutions with brushes or sprayers. Common patina chemicals include ferric nitrate for reddish-brown tones and cupric nitrate for greenish-blue effects.
For surface refinement, sculptors employ various polishing tools. Rotary tools with abrasive attachments help smooth rough areas, while progressively finer sandpapers (from 80 to 600 grit) create uniform surfaces. Buffing wheels with compounds like tripoli and rouge bring out the metal's natural luster.
Chasing tools play a vital role in final detailing. These include specialized hammers and punches that refine texture and remove imperfections. Files and rifflers help perfect contours, while burnishers create smooth, reflective surfaces on highlighted areas.
Protective finishes complete the process. Artists may apply waxes (such as Renaissance or microcrystalline wax) with soft brushes to preserve the patina, or use lacquers for more durable protection. Final inspection often involves magnifying glasses and specialized lighting to ensure flawless results.
These finishing techniques not only enhance the sculpture's visual appeal but also contribute to its longevity, protecting the artwork from environmental factors while showcasing the artist's skill and vision.