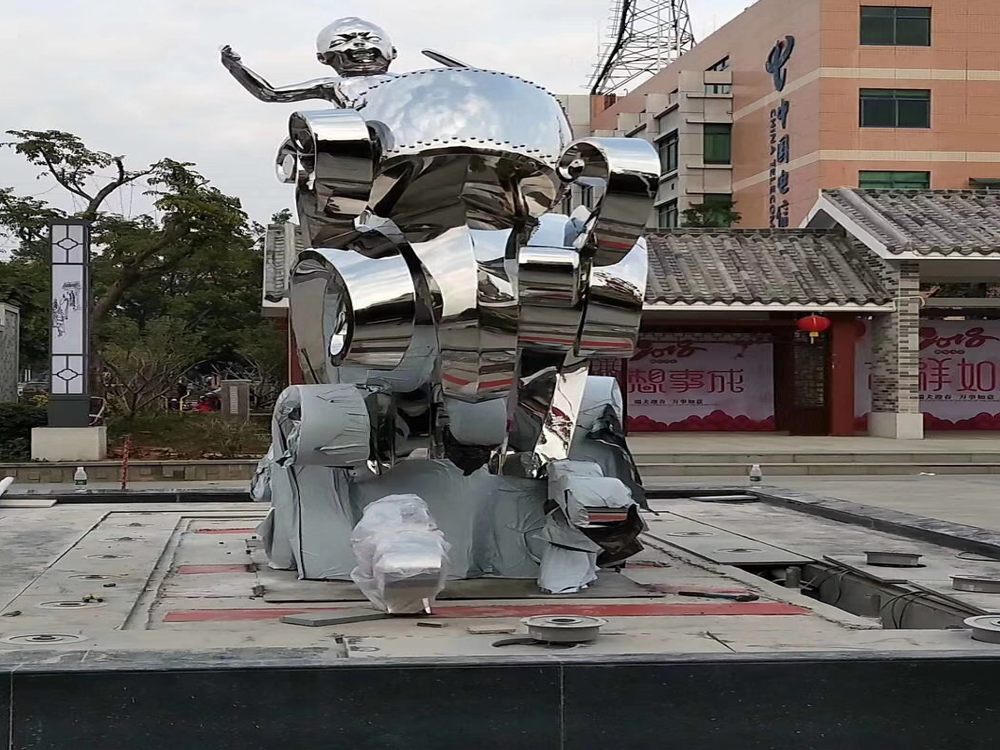
Creating bronze sculptures with thin elements presents unique challenges for sculptors, who must balance artistic vision with structural durability. To ensure integrity, artists employ several specialized techniques.
One common method involves using internal armatures—metal frameworks that provide hidden support for delicate sections. These armatures are often made of stainless steel or bronze rods, carefully shaped to match the sculpture’s design while remaining invisible in the final piece.
During the lost-wax casting process, sculptors may reinforce thin wax elements with additional material or strategic gating systems to ensure even metal flow. Advanced foundries also use controlled cooling methods to prevent stress fractures in slender sections.
Post-casting, artisans may apply heat treatment or mechanical strengthening techniques like peening to enhance durability. Modern sculptors increasingly leverage digital tools, such as 3D modeling and stress analysis software, to predict and address weak points before casting begins.
By combining traditional craftsmanship with innovative engineering approaches, sculptors create breathtaking bronze works where fragile-appearing elements withstand the test of time.