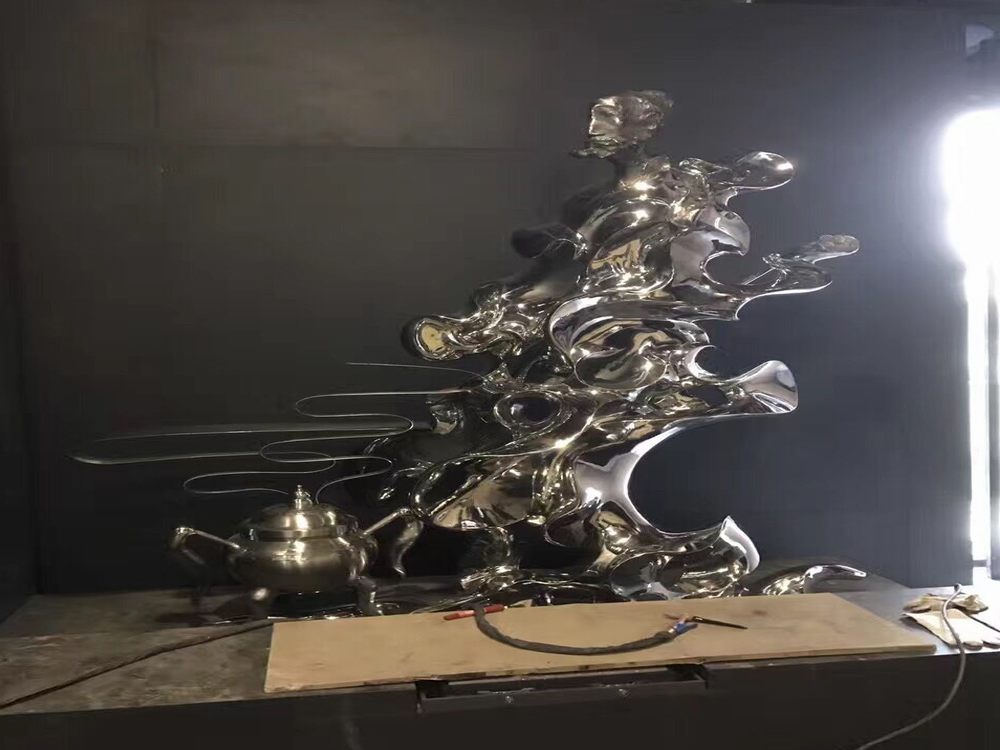
Creating durable joints in large-scale metal installations is critical for ensuring structural integrity, longevity, and safety. The process requires careful planning, precise execution, and adherence to industry best practices. Here are key strategies to achieve robust metal joints:
1. Material Selection: Choose compatible metals and filler materials to prevent galvanic corrosion and ensure strong bonding. High-quality alloys with similar thermal expansion rates are ideal.
2. Joint Design: Opt for joint designs like butt, lap, or T-joints based on load requirements. Reinforcing with gussets or bracing can enhance durability under stress.
3. Welding Techniques: Use appropriate welding methods (MIG, TIG, or arc welding) and ensure proper penetration. Pre-heating thick metals and post-weld heat treatment can reduce residual stresses.
4. Surface Preparation: Clean and degrease surfaces thoroughly to eliminate contaminants. Beveling edges improves weld penetration and joint strength.
5. Quality Control: Conduct non-destructive testing (NDT) such as ultrasonic or X-ray inspections to detect flaws. Regular maintenance checks prevent premature failure.
By following these practices, engineers and fabricators can create metal joints that withstand environmental and mechanical stresses, ensuring the longevity of large-scale installations.