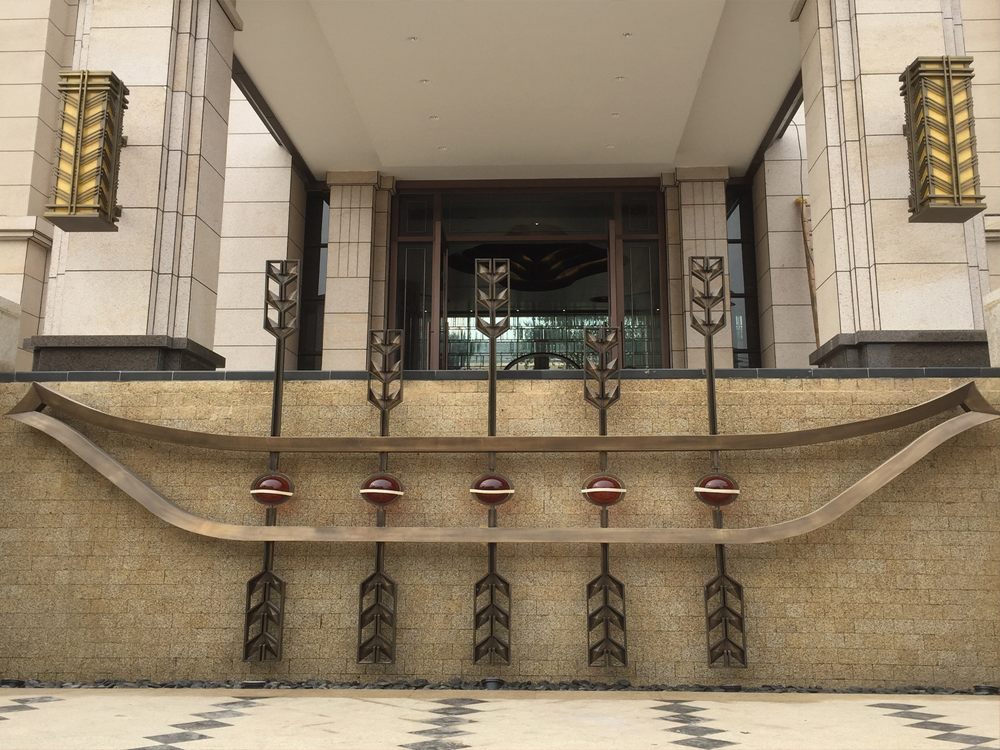
Creating bronze sculptures requires meticulous attention to alloy composition, as even minor deviations can affect durability, color, and workability. Foundries employ several strategies to ensure consistency in bronze alloys, typically composed of copper, tin, and trace elements like zinc or lead.
First, precise raw material selection is critical. Reputable foundries source high-purity metals from trusted suppliers and conduct spectroscopic analysis to verify composition before melting. Batch documentation tracks each material lot for traceability.
During the melting process, computerized induction furnaces maintain exact temperatures, while automated dosing systems add alloying elements with precision. Infrared thermography and real-time spectrometry allow technicians to monitor the molten metal's chemical makeup, making adjustments as needed.
Post-casting, samples undergo laboratory testing including X-ray fluorescence (XRF) to confirm the alloy meets specifications. Many foundries maintain proprietary alloy formulas refined through decades of experience, with some adding unique elements to achieve specific patina responses or mechanical properties.
Quality control extends to the pouring process, where consistent temperature and pouring speed prevent segregation of alloy components. Modern foundries often use robotic pouring systems to eliminate human variability.
By combining advanced technology with traditional metallurgical knowledge, foundries deliver bronze alloys that meet both artistic requirements and industrial standards for sculpture longevity. This rigorous approach ensures each casting maintains the material qualities that make bronze the premier choice for enduring artworks.