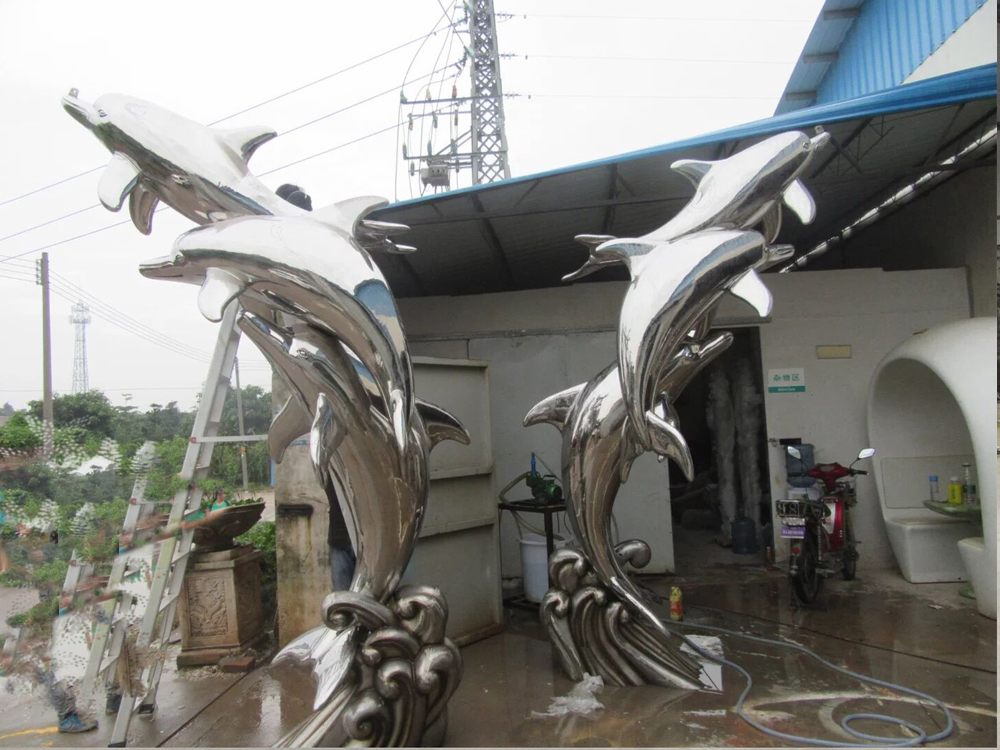
Creating seamless joints in welded metal sculptures requires a combination of technical skill, artistic vision, and meticulous attention to detail. Artists begin by carefully selecting compatible metals and preparing the surfaces to ensure clean, precise welds. Using techniques like TIG (Tungsten Inert Gas) welding, they achieve controlled, precise heat application, minimizing distortion and allowing for smooth transitions between pieces.
After welding, the real artistry begins. Grinding, sanding, and polishing are employed to blend the joints seamlessly into the sculpture’s surface. Artists often use progressively finer abrasives to eliminate visible seams, followed by buffing to match the surrounding metal’s texture and sheen. For a truly flawless finish, some apply patinas or coatings to unify the appearance further.
Advanced sculptors may also employ cold joining methods or hidden internal supports to reduce visible welds. The key lies in balancing structural integrity with aesthetic perfection, ensuring the final piece appears as though it was cast in a single, continuous form. This painstaking process transforms raw metal into elegant, cohesive artworks that captivate viewers with their polished, seamless beauty.