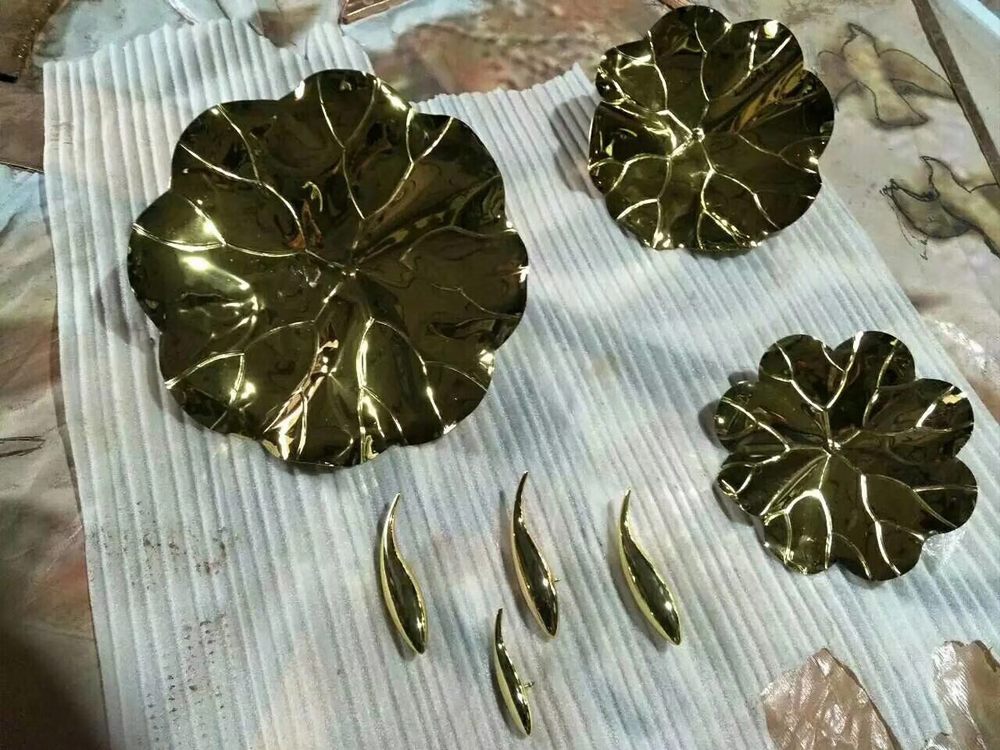
Creating bronze sculptures presents unique challenges, whether artists choose hollow or solid casting techniques. Hollow bronze sculptures require intricate processes like lost-wax casting, where a clay core is surrounded by wax before molten bronze replaces it. This method reduces material costs but demands precision to avoid structural weaknesses. Thin walls can warp during cooling, and improper venting may cause cracks.
Solid bronze sculptures, while more durable, consume significantly more material, increasing expenses. The sheer weight of solid bronze limits size and installation options, often requiring reinforced bases. Cooling solid pieces evenly is critical to prevent internal stress fractures.
Artists must also consider finishing—hollow sculptures allow for internal patina work, while solid pieces require heavier polishing tools. Ultimately, the choice depends on artistic vision, budget, and technical expertise, with both methods offering distinct aesthetic and practical trade-offs.