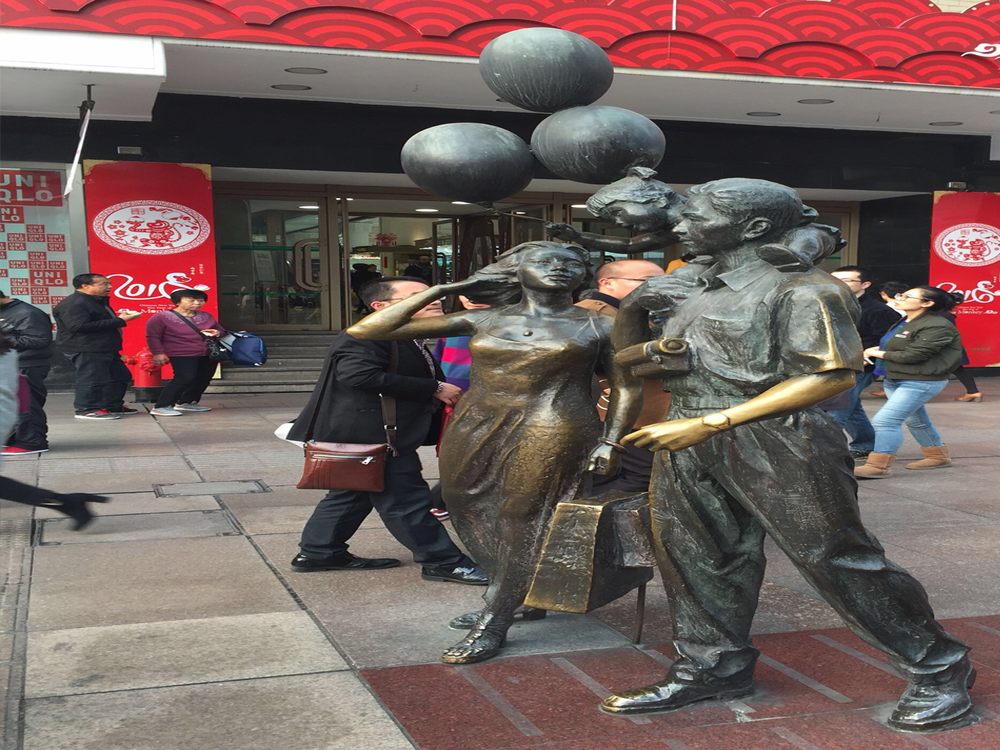
Bronze sculptures with extended limbs present unique challenges in maintaining structural integrity over time. The most common reinforcement methods include internal armatures, which provide crucial skeletal support. Stainless steel or bronze rods are often embedded within the limbs during the casting process, creating an invisible yet durable framework.
For particularly delicate extensions, artists frequently employ cross-bracing techniques. This involves creating strategic connections between limbs or adding discreet support elements that blend with the artwork's design. Many conservators recommend bronze welding at stress points, where additional material can be seamlessly integrated to strengthen vulnerable areas.
Modern approaches incorporate advanced materials like carbon fiber rods, offering high strength-to-weight ratios. These contemporary solutions are especially valuable for large-scale installations where traditional metal armatures might add excessive weight. Proper weight distribution remains paramount, with many sculptors designing counterbalances within the base to offset extended limb leverage.
Regular maintenance inspections help identify stress fractures early, allowing for timely reinforcement. The choice of technique ultimately depends on the sculpture's size, pose, and environmental conditions, with professional conservators often combining multiple methods for optimal longevity.