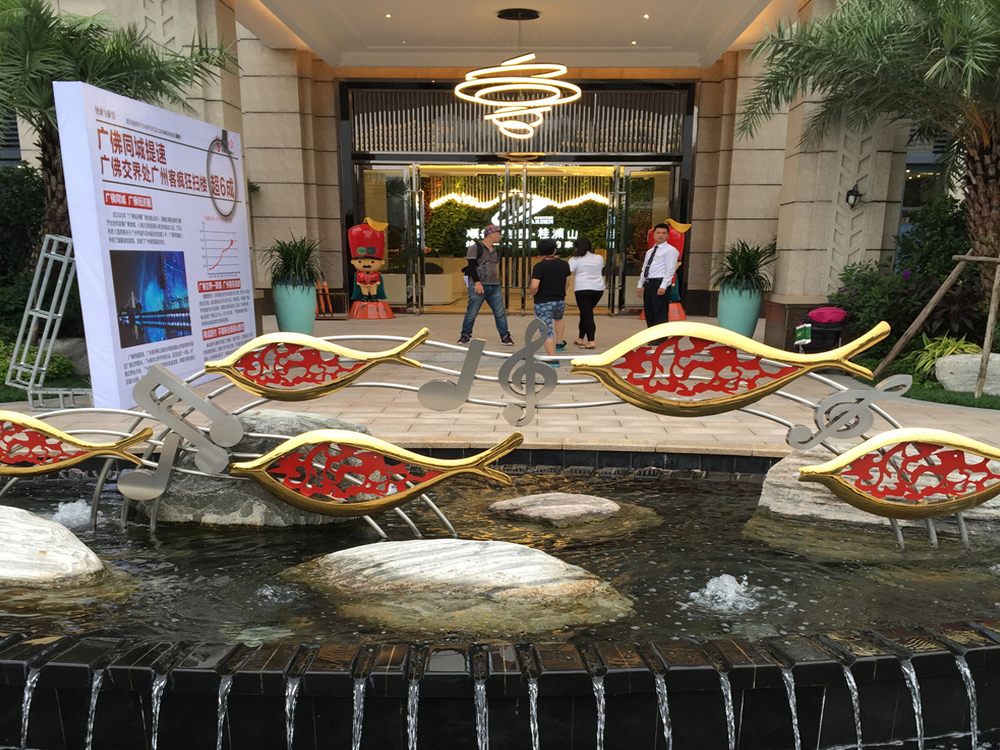
Creating bronze sculptures with a high level of reflectivity is a meticulous process that combines traditional craftsmanship with modern techniques. Artists begin by carefully casting the bronze using the lost-wax method, ensuring a smooth surface free of imperfections. Once cooled, the real magic begins.
The key to achieving mirror-like shine lies in progressive polishing. Artists start with coarse abrasives (60-120 grit) to remove casting marks, gradually moving to finer grits (up to 2000) for smoothing. Between polishing stages, they use specialized compounds like tripoli and rouge to enhance the metal's luster.
Many sculptors employ electroplating techniques, applying thin layers of nickel or chrome before final polishing. This not only increases reflectivity but also protects against oxidation. Some contemporary artists use laser polishing technology for ultra-precise surface refinement.
The final step involves applying protective coatings like lacquer or wax while maintaining the sculpture's reflective qualities. Master artists often develop unique finishing formulas, sometimes incorporating Renaissance-era techniques with modern innovations to create their signature shines.
Maintenance is crucial - reflective bronze requires regular cleaning with pH-neutral solutions and reapplication of protective coatings to preserve its luminous quality for generations. The result is breathtaking sculptures that interact dynamically with light and their environment.