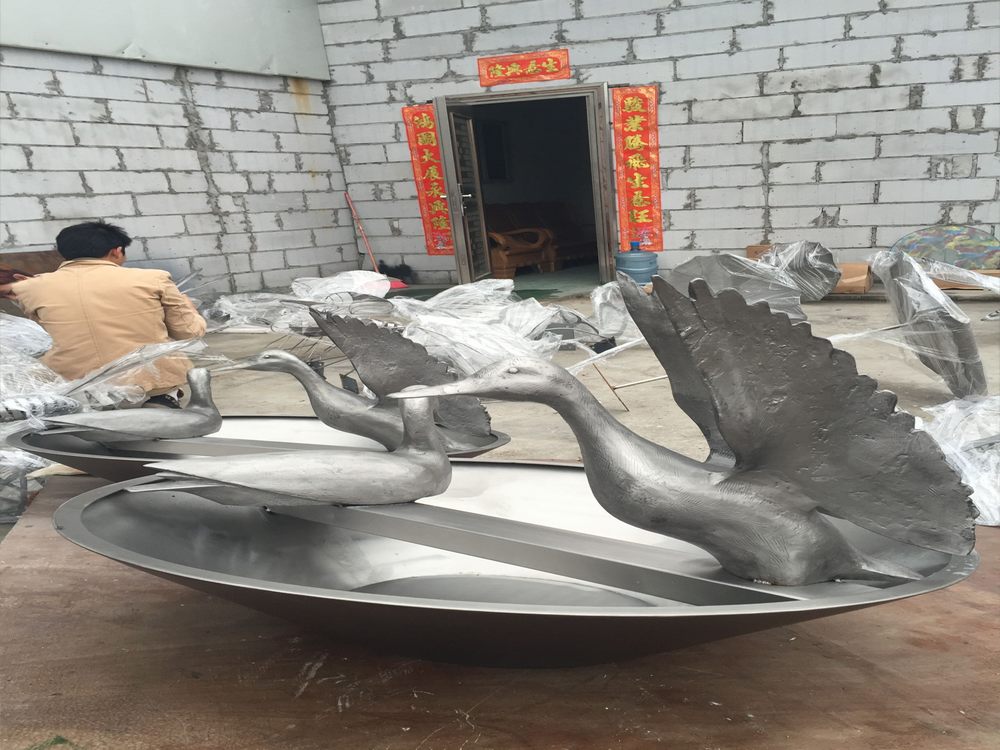
Bronze casting, an ancient art form dating back thousands of years, has undergone remarkable technological transformations in the last five decades. Among the most significant advancements is the integration of 3D printing technology. Modern artists and foundries now use 3D printing to create highly detailed wax or resin models, streamlining the traditional lost wax casting process. This innovation allows for unparalleled precision and complexity in bronze sculptures.
Another breakthrough is the development of advanced ceramic shell techniques in investment casting. These high-strength ceramic molds withstand extreme temperatures, enabling the production of larger and more intricate bronze pieces with fewer defects. Additionally, computer-aided design (CAD) software has revolutionized the planning phase, allowing artists to visualize and refine their designs digitally before casting.
Environmental advancements have also played a crucial role. New eco-friendly binders and recyclable materials reduce the environmental impact of bronze casting, aligning the craft with modern sustainability standards. Furthermore, automated pouring systems and robotic finishing tools have increased efficiency while maintaining the artistry of handmade bronze work.
These innovations ensure that bronze casting remains a vibrant and evolving art form, blending ancient traditions with cutting-edge technology.